Covers protect the carcass of the belt from load abrasion and any other conditions that could contribute to belt deterioration. The top and bottom covers of the conveyor belt provide very little, if any, structural strength to the belt. The purpose of the top cover is to protect the carcass from impact damage and wear. The bottom cover provides a friction surface for driving and tracking the belt. Usually, the top cover is thicker than the bottom cover and more durable for abrasion, impact damage, and wear, due to its increased potential for damage. Abrasion and cutting may be so severe that a top cover as thick as 18 millimeters (0.75 in.) or more is required. In any case, the goal of cover selection is to provide sufficient thickness to protect the carcass to the practical limit of carcass-life.
The aspect ratio of a conveyor belt is the thickness of the top cover in relation to the thickness of the bottom cover.
The covers can be made of a number of elastomers, including natural and synthetic rubbers, PVC, and materials specially formulated to meet special application requirements such as resistance to oil, fire, or abrasion.
Users might be tempted to turn a belt over when the carrying side has become worn. In general, it is better to avoid inverting the belt after deep wear on the top side. Turning the belt over presents an irregular surface to the pulley, resulting in poor lateral distribution of tension, and may lead to belt wander. Another problem is that there may be cargo fines embedded into what was formerly the belt’s carrying surface; when the belt is turned over, this material is now placed in abrasive contact with pulley lagging, idlers, and other belt support systems. In addition, after years of being troughed in one direction, the belt tends to take a “set” (a predisposition to a direction) and will resist the necessary reversing of trough needed to invert the belt. Sometimes this can take weeks to overcome and can lead to belt-tracking problems.
A specific mention must be made of the practice of some belting manufacturers of stamping their logo into the carrying surface of the belt. Even when near the belt edge, this recessed area becomes a trap for conveyed material, and the roughness of the area can abuse the belt-cleaning and sealing which the embossed are will pass, it is recommended that users specify that these supplier logos be positioned on the return, non-carrying side of the belting.
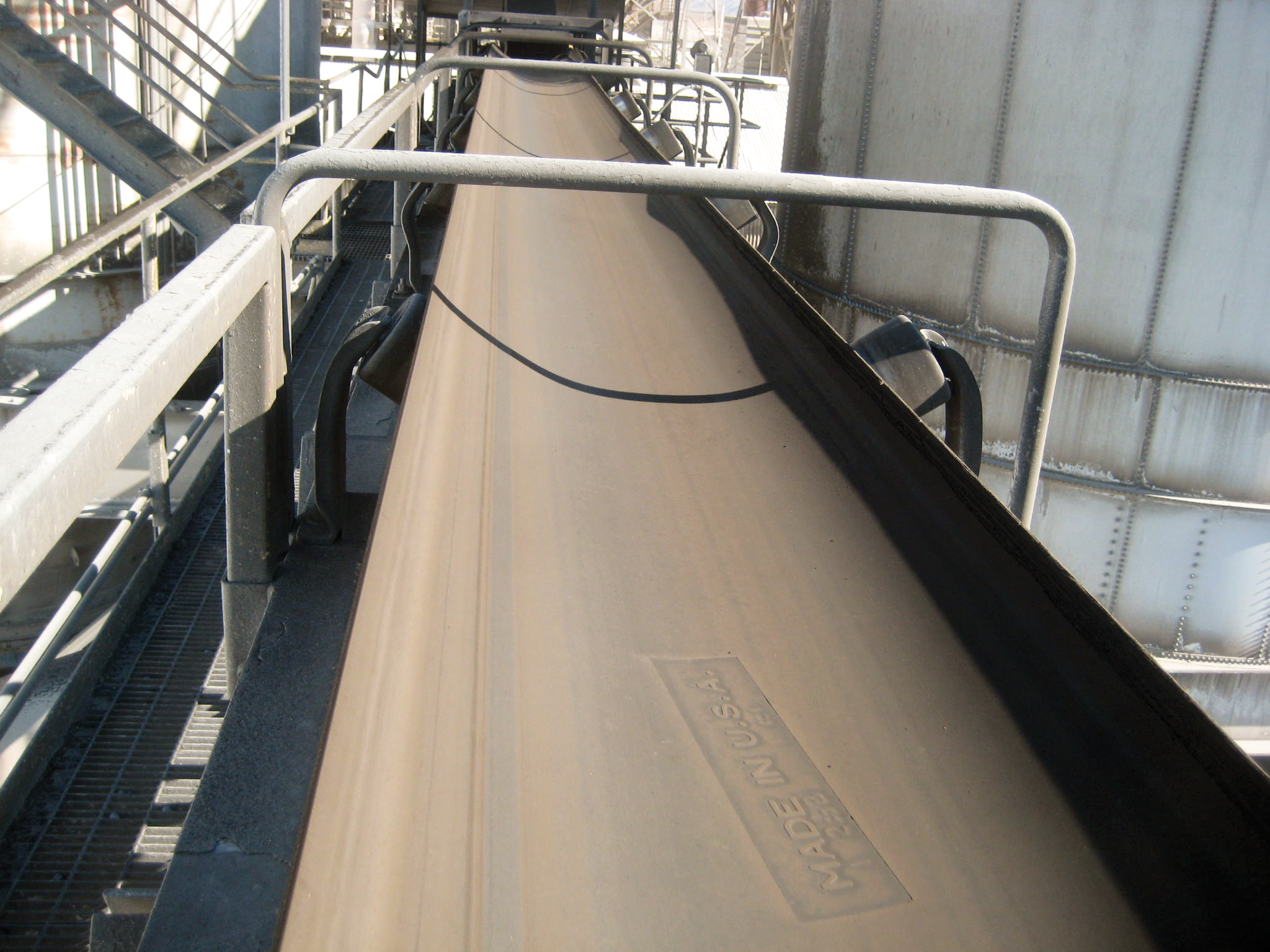
Leave Comment