An operation’s success at eliminating carryback can be categorized into arbitrary “Levels.” Achievement of these levels would be determined by a measurement of the amount of carryback remaining on a prescribed area (usually a square meter) of belting. For the purposes of this discussion, the baseline for carryback material remaining on the belt (or “Level 0” cleaning) would be more than 250 grams of material per square meter.
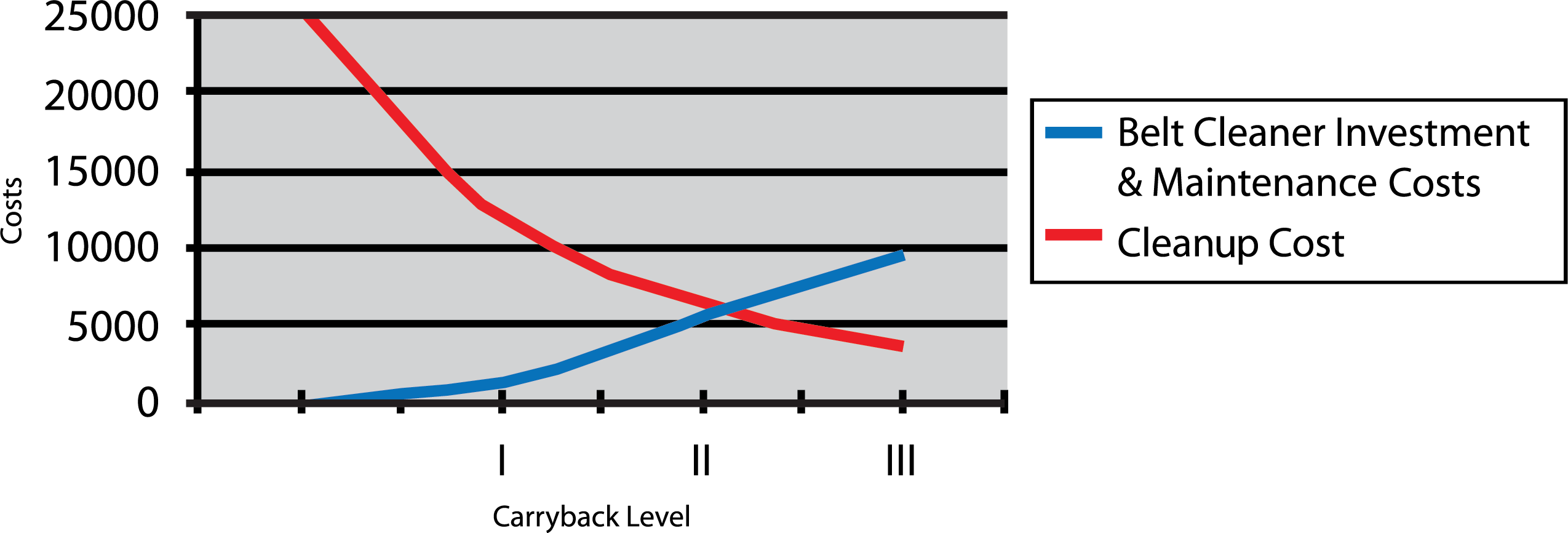
Level I cleaning would be defined as allowing 101 to 250 grams of carryback per square meter to remain on the belt. A typical belt-cleaning system that could achieve Level I cleaning would be a single primary cleaner or a slab-style secondary cleaner.
Level II cleaning is defined as leaving 11 to 100 grams of material per square meter of belting. A typical cleaning system to achieve this level of carryback would be a double or triple engineered cleaner system, composed of a pre-cleaner with a secondary cleaner and sometimes eve a tertiary cleaner.
Level III cleaning is defined as leaving carryback levels between 0 and 10 grams per square meter. A cleaning system that might achieve this level of performance in typical circumstances would be a belt-washing system involving one or several water-spray bars, multiple cleaning assemblies, and a method of removing excess moisture from the belt. These more complicated or sophisticated systems achieve improved cleaning performance; they also cost more to purchase and maintain.
As a company increases its expenditure in belt cleaners, its costs for the cleanup of fugitive material (the carryback released from the belt) will decline. The relationship between the purchase (and maintenance) of cleaning systems and the cost of the additional cleaners will exceed the savings achieved by reducing cleanup expense. The break-even point will be located at the point where the curve of Cleanup Cost intersects with the curve of Belt-Cleaning System Investment and Maintenance Cost.
The point of optimum economic benefit in this example is at or near Level II cleaning performance. Every time the desired level of carryback decreases (or cleaning effectiveness increases), two related costs will be affected: Investment cost increases, while the cost to clean up carryback decreases. As a company increases its expenditure in belt cleaners, its costs for cleanup should decrease. Carryback can be suppressed to nearly zero, but the investment in a belt cleaning system to do that could be greater than can be justified because of the total cost of installing, maintaining, and operating the system. At some point, the cost invested in additional belt cleaners is greater than the savings resulting from the reduced expense for the cleanup of carryback. Consequently, it might be a bad decision, based on the ROI calculation alone, to add additional belt cleaners beyond that point.
Multiple belt cleaner systems take into consideration the dynamics of the surface of the belt and the nature of the material as it passes around the head pulley.
There could be a similar cost versus benefit analysis performed for maintenance and adjustment on belt-cleaning systems. Cleaning performance will be better each time the cleaning blades are clean and re-tensioned against the belt; however, at some point along the line, the labor cost will be greater than the value of the improved performance. As an example, the benefit of weekly inspection and adjustment of cleaning systems might pay for itself, whereas the labor cost of adjustment on an every shift or every day schedule might not.
Of course, this is a purely economic evaluation of the benefit of improvements in belt-cleaning systems. It does not include any variable for health, safety, or community-relations issues. There is no universal answer to these questions: the balance between health and safety, maintenance costs, and the return on investment must be evaluated and optimized for each plant.
Leave Comment