The basics for installing an effective belt-cleaning system include the following criteria: far forward, out of the material flow, and with minimal risk to the belt.
Far Forward
To minimize the release of carryback into the plant, belt cleaning should take place as far forward on the conveyor’s return run as possible. Typically, at least one cleaner is installed at a point where the belt is still in contact with the head pulley. Normally, this cleaner is installed on the face of the head pulley, just below the point where the material leaves the belt. This position, called the primary position, provides a significant advantage in that the carryback is immediately returned to the main material flow. This reduces the potential for release onto rolling components and into the plant environment. With the cleaners tensioned against the belt and the belt still against the head pulley, control of the blade-to-belt pressure is more precise. The head pulley provides a firm surface against which to mount the cleaner.
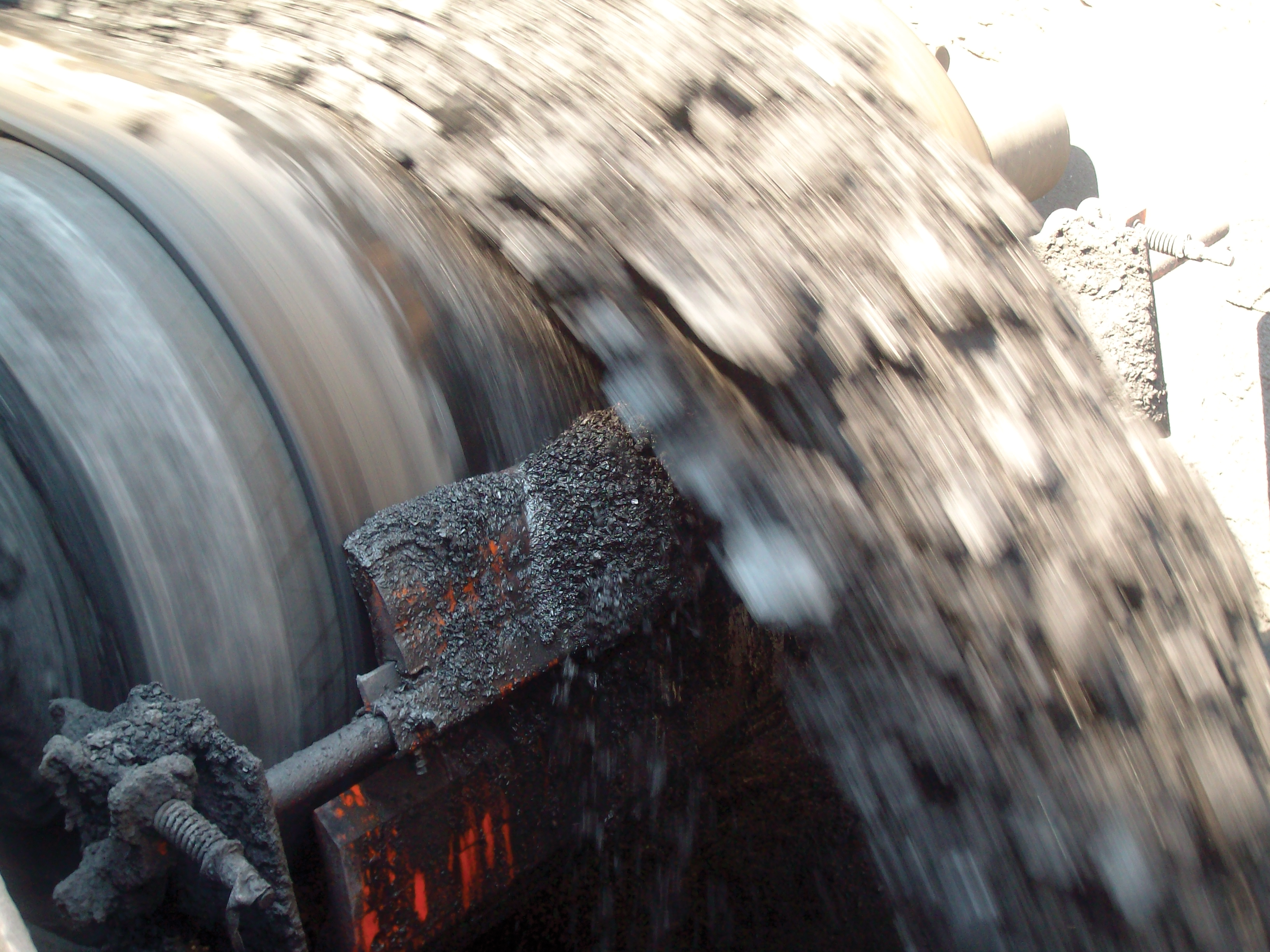
Utilizing the space available and mounting the first cleaner in what is considered the primary position creates more space available for the installation of one or more cleaners in the secondary and tertiary positions. As with the primary cleaner, the farther forward each added cleaner is installed, the less chance there is for carryback to escape and the less need there is for devices like dribble chutes or scavenger conveyors to return recovered material to the flow.
Out of the Material Flow
It is important that cleaners are installed out of the flow of the material and that the material cleaned from the belt does not adhere and build up on the blades or structure.
A cleaner installed in the trajectory of the material may experience premature wear on the support frame and the back of the blades, making it necessary to change the blades before the cleaning edge is worn out. Preferred placement of a cleaner in the primary position involves installing the cleaner so the blade tip is below the horizontal centerline of the pulley.
A cleaner installed outside the material trajectory can still acquire a buildup of material that adheres to its outside surfaces. Cleaners should be designed to minimize the chance for material adhesion. This is accomplished by avoiding flat surfaces and pockets that can capture material and by utilizing non-stick materials for cleaner construction. In the proper environment, water sprayed on the surface of the belt, or on the cleaners, assists in softening the material and minimizing material buildup.
Multiple belt cleaner systems take into consideration the dynamics of the surface of the belt and the nature of the material as it passes around the head pulley.
With Minimal Risk to the Belt
An essential consideration in the selection of a belt-cleaning device is minimizing any risk that the cleaner could damage the belt or a splice, the very systems it was installed to protect. Belt-cleaning systems must be designed so the blade is capable of moving away from the belt when a splice, damaged section of the belt, or other obstruction moves past the cleaner with the belt. The cleaner’s tensioning systems, particularly on the primary cleaner where the angle of attack is more acute, should include a mechanism to provide relief from the shock of the splice impact.
An aggressive primary cleaner with a lot of cleaning pressure will have a tendency to more quickly wear away the top cover of the belt. These cleaners inherently provide an increased risk of catching on a protruding splice or flap of belt.
Care should be taken in choosing an appropriate material to put in contact with the belt. Material such as strips of used belting should never be applied as a belt-cleaning or sealing material, because they may include steel cables or abrasive fines. These embedded materials cause excessive wear of the belt’s top cover.
Leave Comment