Following design principles that establish safe, service-friendly, and easy-to-clean belt conveyor systems leads to better and more productive operating systems. A cleaner, safer operation is normally a more productive operation in the long run. Safety issues normally correspond to unsafe operating conditions, which are also detrimental to the equipment. Airborne dust can find its way into lungs and bearings; material can accumulate under and on walkways and conveyors, leading to slip, trip, and fall hazards. These unsafe operating conditions are not only hazards to health, but also to the condition of the conveyor equipment. When equipment is shut down for unscheduled repairs, it cannot be productive.
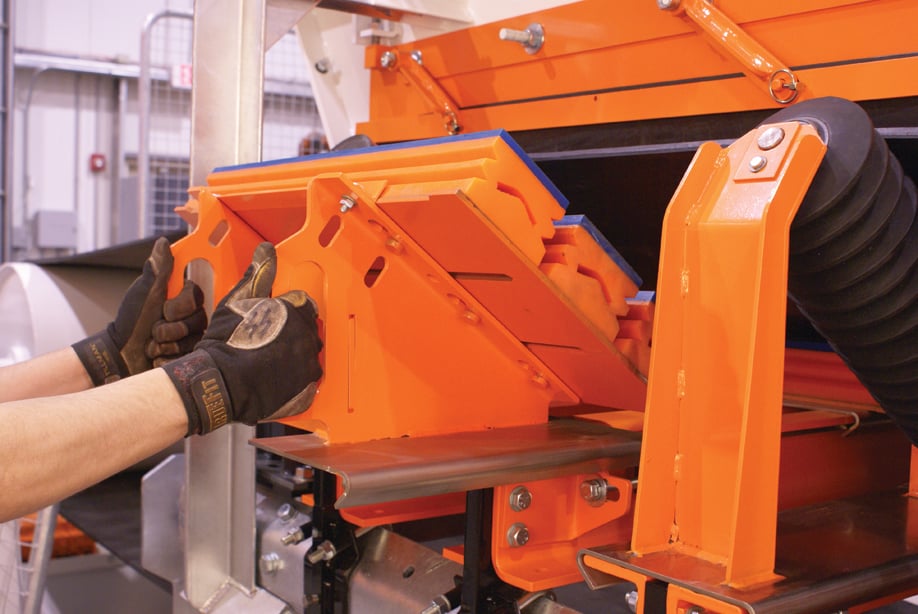
Cost Effective
The total cost of ownership, including the cost per kilogram (per pound) of dealing with fugitive material releases, should be considered in making design and purchasing decisions. Unfortunately, the lowest-bid process discussed earlier, which considers only initial purchase price, has slowed the evolution of clean, safe, and productive designs. While initial purchase price may be lower for a system with no adjustment capabilities and no consideration for future wear-component replacement, the higher costs required to properly install and maintain components, clean up fugitive materials and cover additional equipment downtime will far exceed the costs of a system which takes these factors into consideration in the initial design.
Utilizing standard components where possible in the design may make economic sense, because some economy of purchase may be realized. With some forethought and some slight design changes, standard components (structure, cradles, skirting, ect.) can often be adapted to these new design principles. Use of standard components can provide for ease of installation and replacement due to standardization across the plant. Designing the system for ease of upgradability, buy making components track mounted and service-friendly, can reduce down time and control fugitive materials.
Martin Engineering's Foundations™ book is a comprehensive resource on belt conveyor operations and maintenance.
Upgradeable
Designers routinely consider capacity upgrades, but they rarely include provisions for component upgrades. A track-mounted system provides flexibility for quickly installing different problem-solving components. The use of a pre-engineered mounting hole pattern in the structure around the conveyor’s transfer point allows for the installation of a new or improved system quickly and easily. A uniform-hole pattern for accessory mounting will encourage component suppliers to adapt modular, bolt-on or clamp-on designs for easy retrofits. Utilizing structural platform designs- which incorporate tracks, modularly and easy retrofitability – will encourage designers to continue to modernize the way bulk materials are handled today and in the future.
Leave Comment