The Process for Developing a Wash-Box System
When developing a belt-washing station, it is desirable to provide a complete system analysis that takes into account a number of factors including the physical layout of the conveyor and water-recycling system, the amount of energy required for drying and water recycling, and the ability of the solids to be separated from the water.
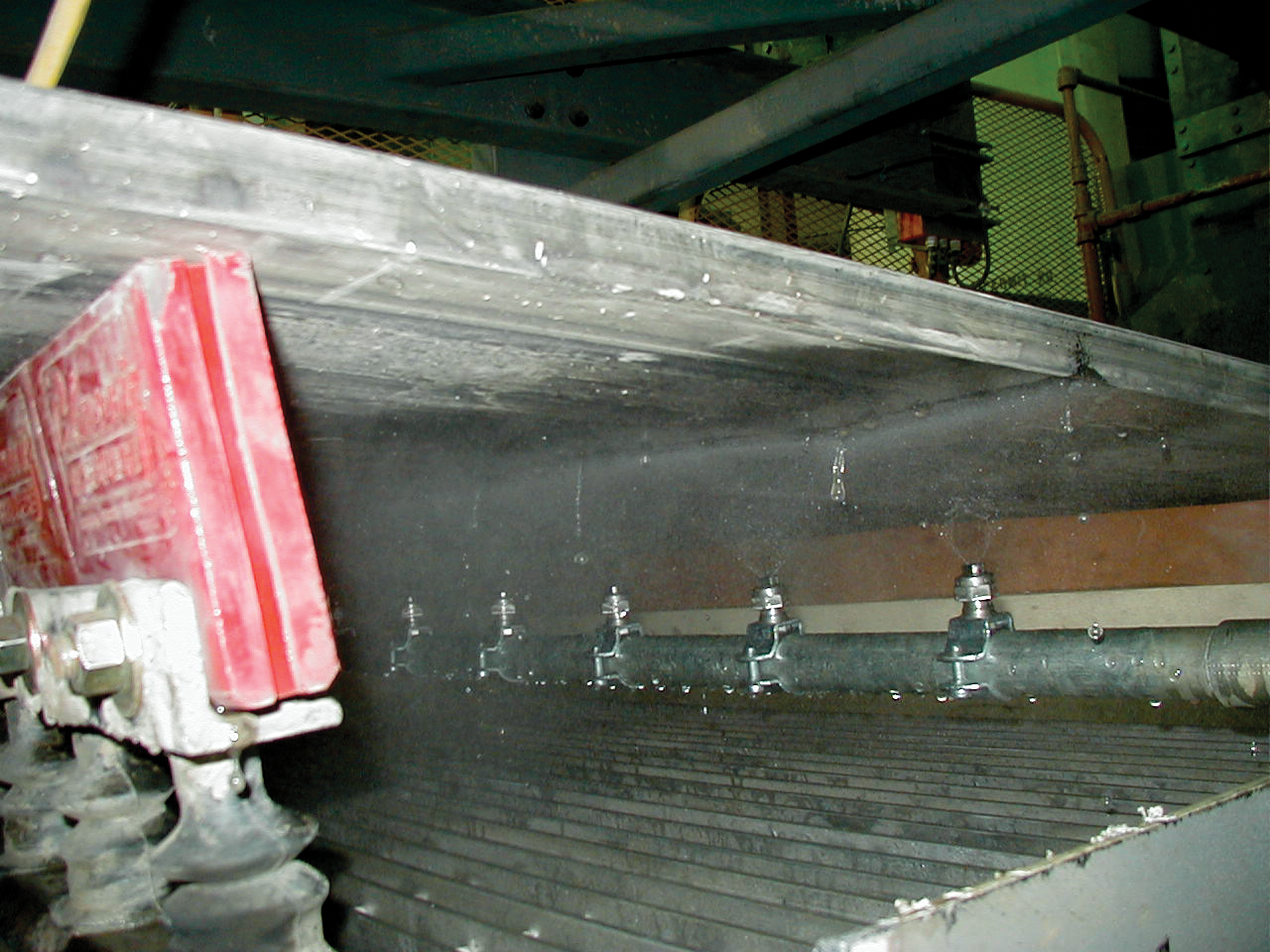
When considering the installation of a wash box, there are a number of questions that must be considered. These include:
- How much water will the wash box use?
- How clean will the belt be as it enters the wash box?
- How clean must the belt be as it leaves the wash box?
- How dry will the belt be?
- What will be done with the effluent (the mix of solids and water)?
These questions can be answered with reasonable accuracy if there is detailed information available about the properties of the bulk material, the belt and bulk material interface conditions, the amount of carryback present, and the general choice of equipment in the wash box.
Typical Specifications
A. Spray-wash system
The conveyor system will be equipped with a spray belt-washing system installed directly after the head chute to provide final removal of any residual cargo from the belt. This spray-wash system will be contained in a watertight metal enclosure fitted with water supply and an oversized drain.
B. Size
The belt-washing system will be sized based on the amount and properties of expected carryback per square meter (/ft2) of belt.
C. Water-spray bar
The enclosure shall be fitted with at least one water-spray bar with engineered nozzles that are positioned to wet the entire cargo-carrying portion of the belt and to flush removed material out of the box through the drain.
D. Secondary cleaners
The wash box will be fitted with a minimum of two secondary cleaners to remove fines and water from the belt’s load-carrying surface.
E. Access
The wash box shall be fitted with watertight access door(s) to allow easy inspection and service.
F. Hold-down rollers
The spray-wash system shall include a minimum of three hold-down rollers above the belt that hold the belt in position against the spray-applied water and cleaning edges.
G. Drain system
The volume and flow rate of flushing water and design of the drain system shall be sufficient to prevent settling of bulk solids in the drain system.
Leave Comment