In General
- It is important to design conveyor belt-cleaning systems for the problems presented by the “worst-case” material conditions, rather than for “normal” operating conditions. This will allow cleaning systems to better handle changes in the materials
- Belt cleaners should be installed as close to the material discharge point as possible, ensuring effective cleaning by supporting the cleaning elements against a firm surface.
- Belt cleaners should be installed outside the material trajectory and positioned so that cleaned materials cannot build up on the blades and structures.
- Belt-cleaning systems should be designed to provide less than full-belt width coverage and allow for minor variations in belt tracking and provide optimum blade-to-belt contact.
- Each head pulley should have a belt cleaning system consisting of (at minimum) a primary cleaner and a secondary cleaner with provisions for the addition of tertiary cleaners.
- The cleaning systems shall be designed to allow simple maintenance and blade-replacement procedures. Periodic maintenance should be performed as per manufacturers’’ recommendations to keep the belt cleaners operating at peak performance.
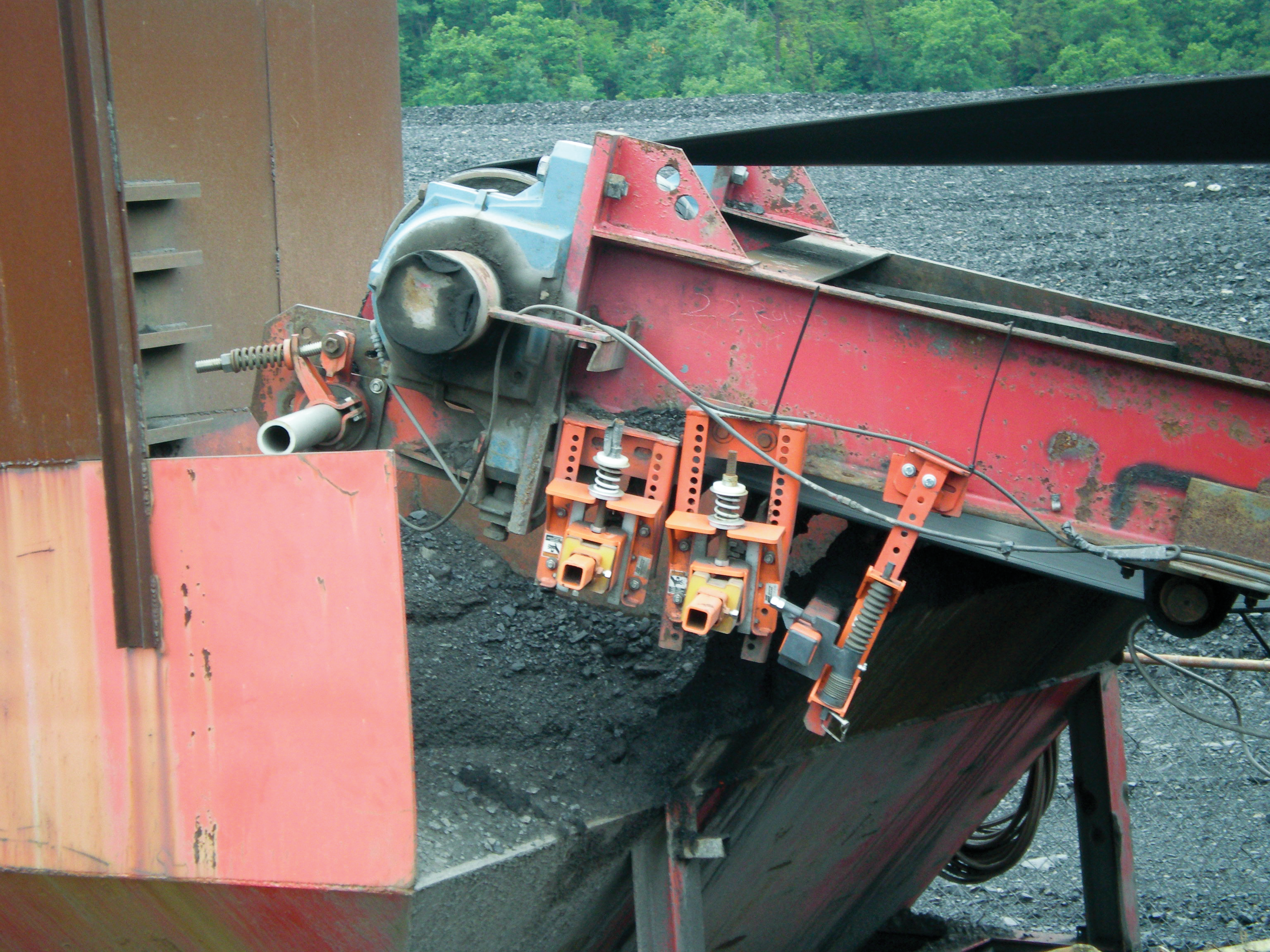
Primary Cleaners
- Primary cleaners perform the initial rough cleaning. They should be designed with flexible (elastomer) blades and radial-adjustment tensioning devices.
- Primary cleaners should be installed on the face of the head pulley just below the trajectory of the material, utilizing a positive-rake cleaning angle.
- Primary-cleaner blades should incorporate a constant-cleaning angle and area design.
- Pre-cleaners should be designed for use on one-directional and reversing belts.
- Reversing belts should have a pre-cleaner installed on each discharge pulley.
There are a few key specifications to consider when choosing the appropriate belt cleaner for your belt conveyor.
Secondary Cleaners
- Secondary cleaners remove the majority of the material that passes by the pre-cleaner’s blades. Secondary blades should contact the belt just past the point where the belt has left the head pulley. Alternatively, the cleaners can be located behind the head pulley with a hold-down roll above the blades. The hold-down roll should be a minimum of 100 millimeters (4 in.) in diameter.
- Secondary-cleaner blades should be designed to contact the belt in a negative-rake position.
- The blades should be constructed of tungsten carbide or similar abrasion-resistant material.
- On one-directional belts, the cleaners should be adjusted with a radial adjustment tensioning device, and on reversing belts with a vertical-spring tensioner.
- Reversing belts should have a reversing secondary cleaner installed as close as possible to each terminal (discharge) pulley.
Multiple belt cleaner systems take into consideration the dynamics of the surface of the belt and the nature of the material as it passes around the head pulley.
Tertiary Cleaners
- Space should be planned in the design of conveyor load zones for the possible addition of tertiary cleaners.
- Tertiary cleaners should utilize a separate dribble chute or scavenger conveyor to return to the carryback to the main material flow.
Other
- Necessary utilities (water, electricity, compressed air) should be available at points convenient to the belt-cleaner installation.
- Clearances and access in accordance with CEMA recommendations should be provided in the conveyor design.
Leave Comment