Wear liners play several important roles in increasing the effectiveness and longevity of low-spillage transfer points.
Perhaps most importantly, as indicated by the name of the component, wear liners provide a “sacrificial surface” to suffer the abrasion of conveyed materials. Damage to these components is generally less of a concern than with chute walls, the skirtboard or the skirting seal, since wear liners are comparatively easy to replace.
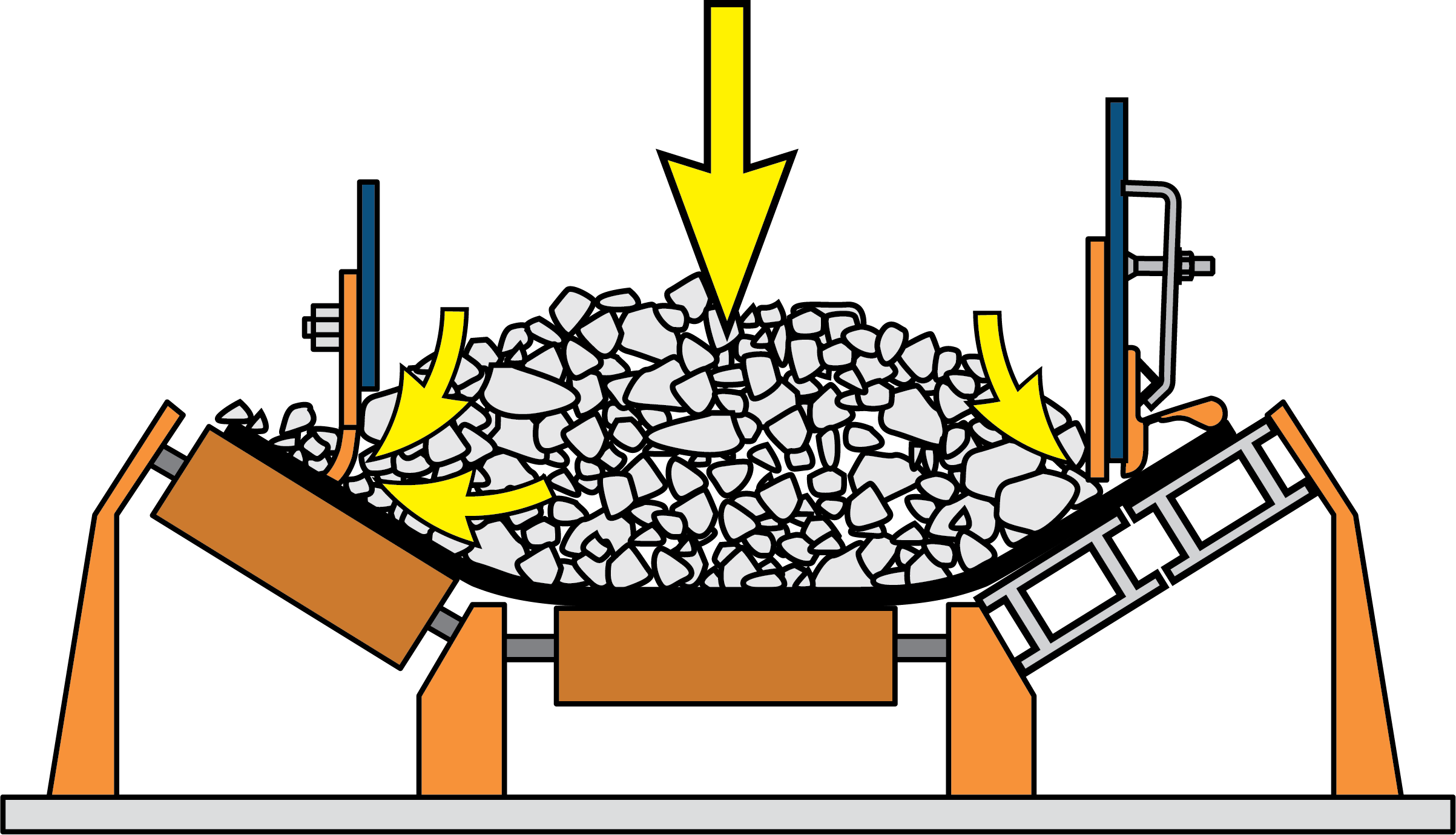
Some wear liners are also designed to reduce friction, impact, noise and the degradation of bulk material.
Wear liners serve as more than just strips of material, however, and can help to center cargo on the conveyor. This also serves to reduce the pressure materials place on the sealing strips, which can significantly improve their lifespan.
The forces of material flowing through a transfer point and dropping onto a belt inside a traditional transfer area create tremendous outward pressures. This side pressure of the material, if uncontrolled, will push material fines and dust away from the center of the material pile under the skirtboard, resulting in spillage and increased wear on the skirting seal. The wear liner adds another solid layer between the materials themselves and the sealing strip, as well as other more sensitive components.
Wear liners reduce the escape of fugitive material from transfer points.
Wear liners are installed along the inside of the skirtboard, serving to protect the skirting seal and the skirtboard itself. This added layer helps to separate the task of load placement from sealing the chute to ensure that components are put only to the task for which they were designed as much as possible. By creating a dam between the material pile and the edge-sealing strips, the wear liners greatly reduce the side loading forces that reach the sealing strips. This arrangement improves the effectiveness and life expectancy of the sealing system while reducing the risk of damage by material entrapment.
While wear liners will prove useful for most low-spillage transfer points, there are certain circumstances where they are not always necessary. Lightly-loaded, where outward pressure is less of a concern, and belts carrying non-abrasive, low-density materials might not need wear liners. In all other circumstances, properly installed and maintained wear liners will reduce the material side-loading forces to increase sealing efficiency and sealing-strip life.
Leave Comment