Pulley Sizes
For decades, tail, bend and discharge pulley sizes have been selected from tables published by belting manufacturers with minimum pulley diameters based on minimizing costs and providing safe stress levels for the belt. Determining the correct size of pulleys should include consideration of ease of access for service. A larger diameter pulley one with a minimum pulley diameter of 600 millimeters (24 inches) would allow adequate space between the carrying and return runs for installation of a tail pulley protection plow and, if necessary, a return belt plow. The additional space that would be supplied between the carrying and return runs of the belt allows for easier inspection of plows and provides adequate space for the plows to eject fugitive materials from the belt. A larger head pulley at the belt discharge provides needed space for installing belt cleaners in the optimal working position. The added cost of adding larger pulleys is offset by the cost savings derived by effectively controlling fugitive materials and by requiring shorter down times and less maintenance.
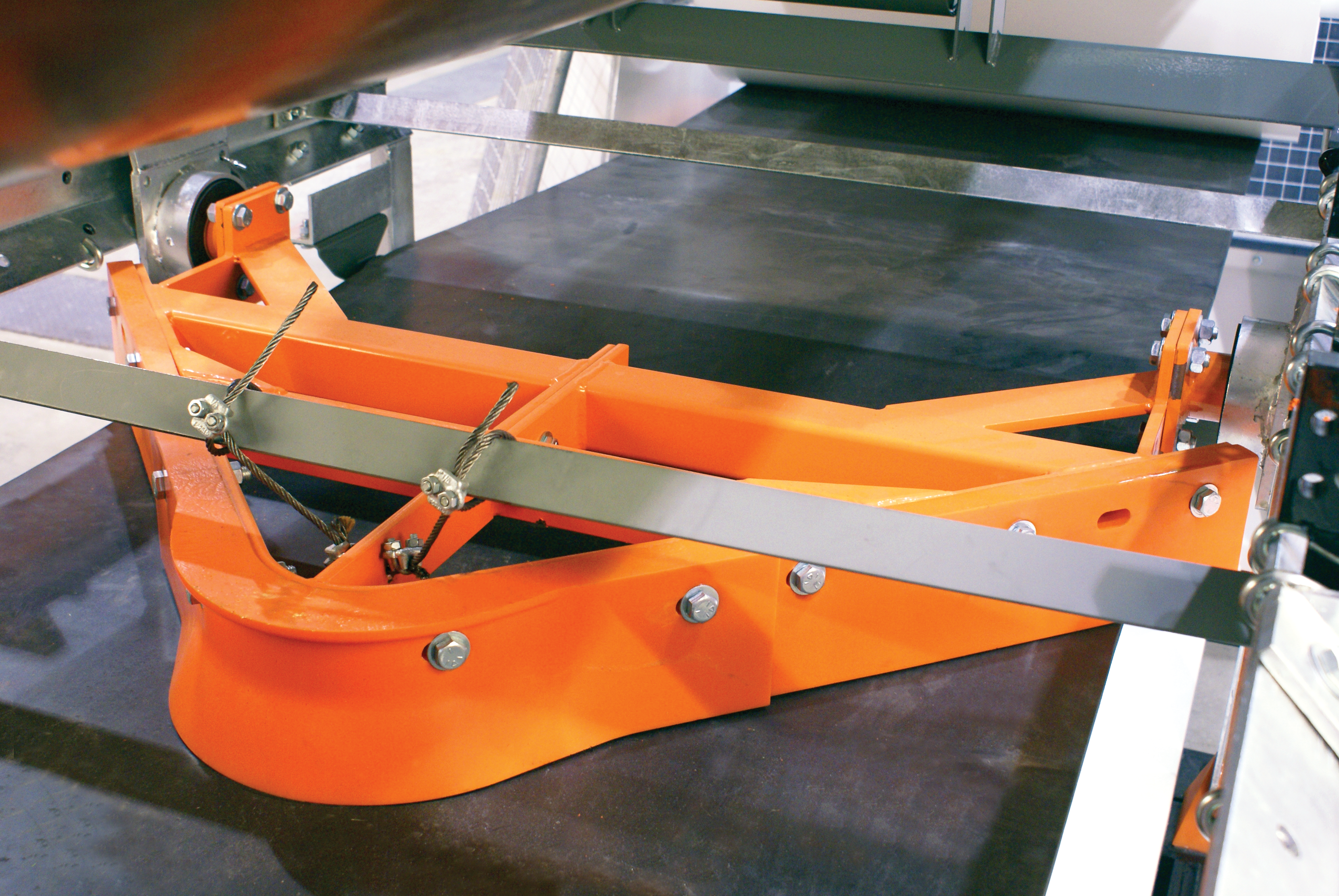
Indexing Idler
Belt mistracking is a major cause of spillage; therefore, much attention is given to belt training devices in order to keep the belt centered in the structure. In an effort to keep the overall cost of a new installation down, training idlers are often supplied in lieu of belt training devices on many new installations. Training idlers often end up tied off to one side or the other in an attempt to either compensate for a situation beyond the capability of the device or protect the device from excessive wear due to the belt continuously running to one side.
Conveyor belts often run to one side or the other due to conditions such as off center loading, conveyor structure alignment issues, conveyor component alignment problems, weather conditions or a variety of other factors. Loose pieces of wire or rope, used to tie off training idlers, in the vicinity of the moving belt are safety hazards. This issue can be exacerbated by changing conditions or operator preferences that require an indexing idler tied off to hold the belt in one direction in the morning to be switched to tie off the belt in the opposite direction in the afternoon.
In the absence of properly aligning the conveyor structure, replacing and/or aligning conveyor components that are causing belt alignment issues, ensuring the load is properly centered or installing one or several belt training devices to properly align and track the belt, these training idlers can be fitted with a mechanism that allows them to be "indexed," or locked into position, without resorting to unsafe wire or rope tie downs.
Martin Engineering's Foundations™ book is a comprehensive resource on belt conveyor operations and maintenance.
Conduit and Piping
Conveyors provide convenient paths for running utilities and electrical components. For decades, utilities and electrical piping have been installed along the conveyor’s structure with little regard to the effects of this location on the installation, maintenance and operation of conveyor components. This issue is particularly noticeable in the discharge and loading zone areas of the conveyor belt system. For example, it is common to see plows buried behind a web of conduit that was installed after the plow was positioned. Plows need to be able to eject foreign objects from the conveyor in the location selected by the designer.
The utility conduits in the discharge and load zones in particular should be run in locations where they do not interfere with access to components that are essential to the control of fugitive material. The main conduit could be run overhead with flexible conduit dropped down where required to provide power to or communicate with the components. Along the carrying run of the conveyor, the structure can be used for supporting conduits as long as the conduit does not interfere with access for service or reduce the effectiveness of the individual components.
See also: Clean Belt Conveyor Design Part 1
Leave Comment