Linear vibrators activate the material inside a chute or bin by using heavy blows on the outside of the structure’s steel walls. In fact, the earliest form of vibration was a hammer. The act of pounding on the chute or bin wall overcomes the adhesive force between the material and the wall surface. However, this hammering on the bin or chutewall often leads to damage to the wall surface. The marks left on the wall by the hammer, often called “hammer rash,” will continue and expand the problem the blow of the hammer was supposed to overcome. In addition, the swinging of the sledgehammer poses the risk of injuries to plant personnel. The piston vibrator was developed to produce this effect without actually swinging a hammer.
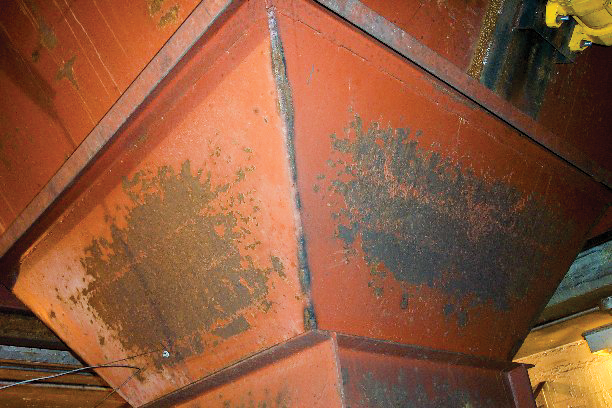
A pneumatic piston (or linear) vibrator uses plant air to move a piston back and forth inside a casing. In some vibrators, this piston may strike the wall; in other designs, it merely oscillates with enough mass to flex the wall. In both cases, the vibrator provides energy through the wall to the material inside the structure. This force—more controlled than a hammer strike—breaks the adhesion between the material and the wall, so the material will flow out of the structure.
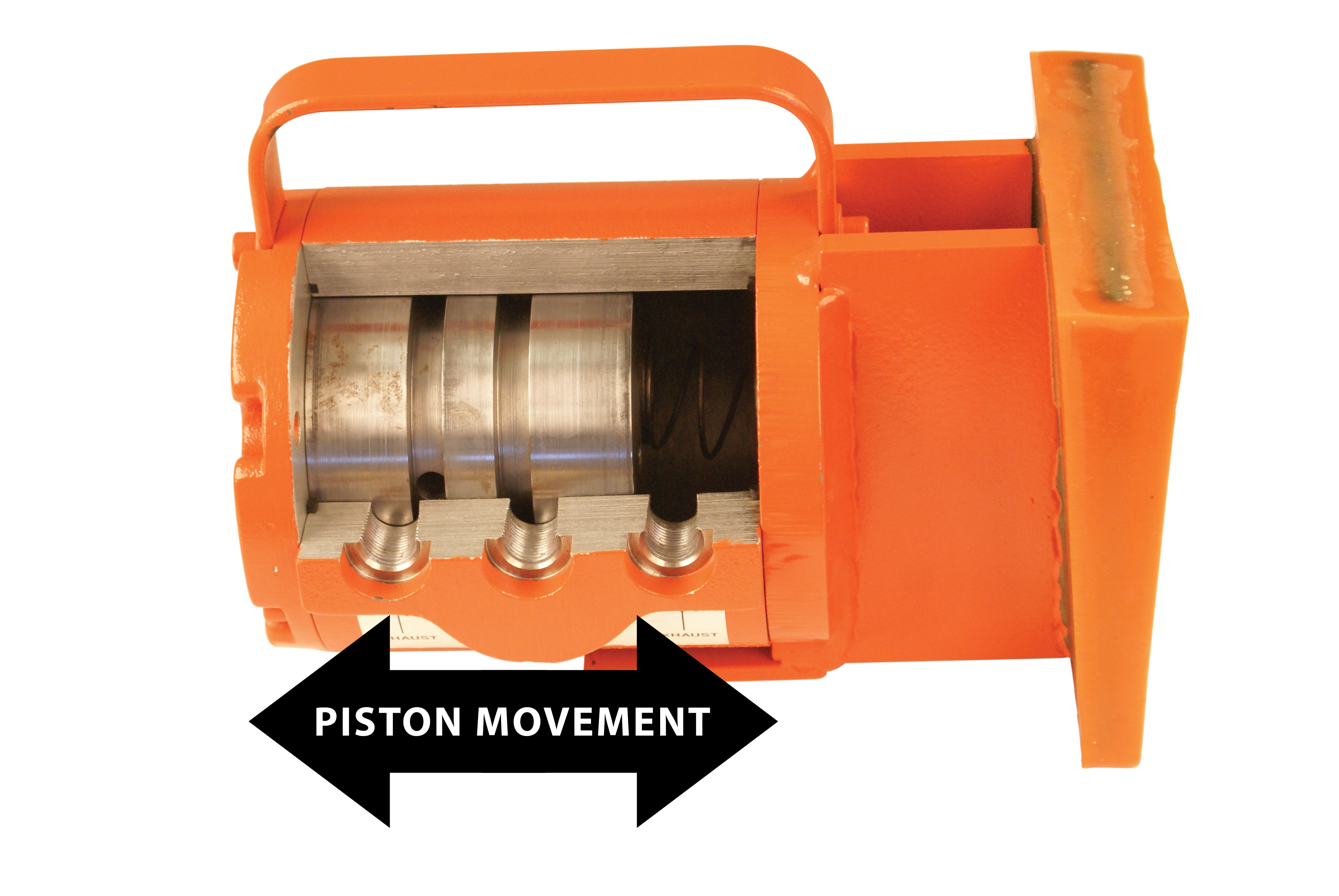
Linear vibration is the best solution for sticky, coarse, high-moisture materials. A convenient test is to take a handful of material and squeeze it into a ball. If the material readily remains in the ball after the fist is opened, linear vibration is probably the best choice.
A piston vibrator would be mounted on the outside of the vessel or chute at the point of the buildup or blockage on the inside. Often these vibrators are attached to a steel channel that is mounted on the chutewall. This mount spreads the force out over a larger area of the structure to maximize the efficiency while preserving the structure from fatigue. Most linear vibrators are driven by plant air and can be controlled remotely, with a solenoid, or locally, with a manual on/off valve.
The vibrator for a particular application is selected according to the weight and characteristics of material in the chute or sloped portion of a bin or hopper. The general “rule of thumb” for typical vibrator applications is to apply 1 newton per 1 kilogram (1 lbf / 10 lbm) of material weight inside the chute. This general rule assumes that the material is flowable and has a density less than 1,440 kilograms per cubic meter (90 lbm / ft3). More force will be needed for materials of high density or moisture or of low density. While the ratio above is acceptable for materials between 640–1440 kilograms per cubic meter (40–90 lbm / ft3), materials with higher or lower bulk densities require different ratios.
The length of the mounting channel and the chutewall thickness best suited for these applications are also dependent on material weight and characteristics; applications outside the parameters given in the table may require specialized engineering. The calculation of linear force is required for application of a vibrator on a chute.
After installation, air-powered vibrators must be tuned to the needs of the application by adjusting the air pressure and/or flow rate to maximize the effect on the bulk material.
Leave Comment