For many years, belt cleaners were homemade affairs, often a slab of rubber, a leftover piece of used belting, or a discarded piece of lumber wedged into the structure or held against the belt by a counterweight. These systems proved to be unwieldy, cumbersome, and generally ineffective. Plant operating requirements necessitated the use of wider, faster, more deeply troughed, and more heavily-loaded conveyors. These requirements led to the development of engineered belt-cleaning systems to protect the plant’s investment by extending the service-life of expensive belts and other conveyor components. These systems usually consist of a structural support (mainframe), cleaning element (blade), and tensioner.
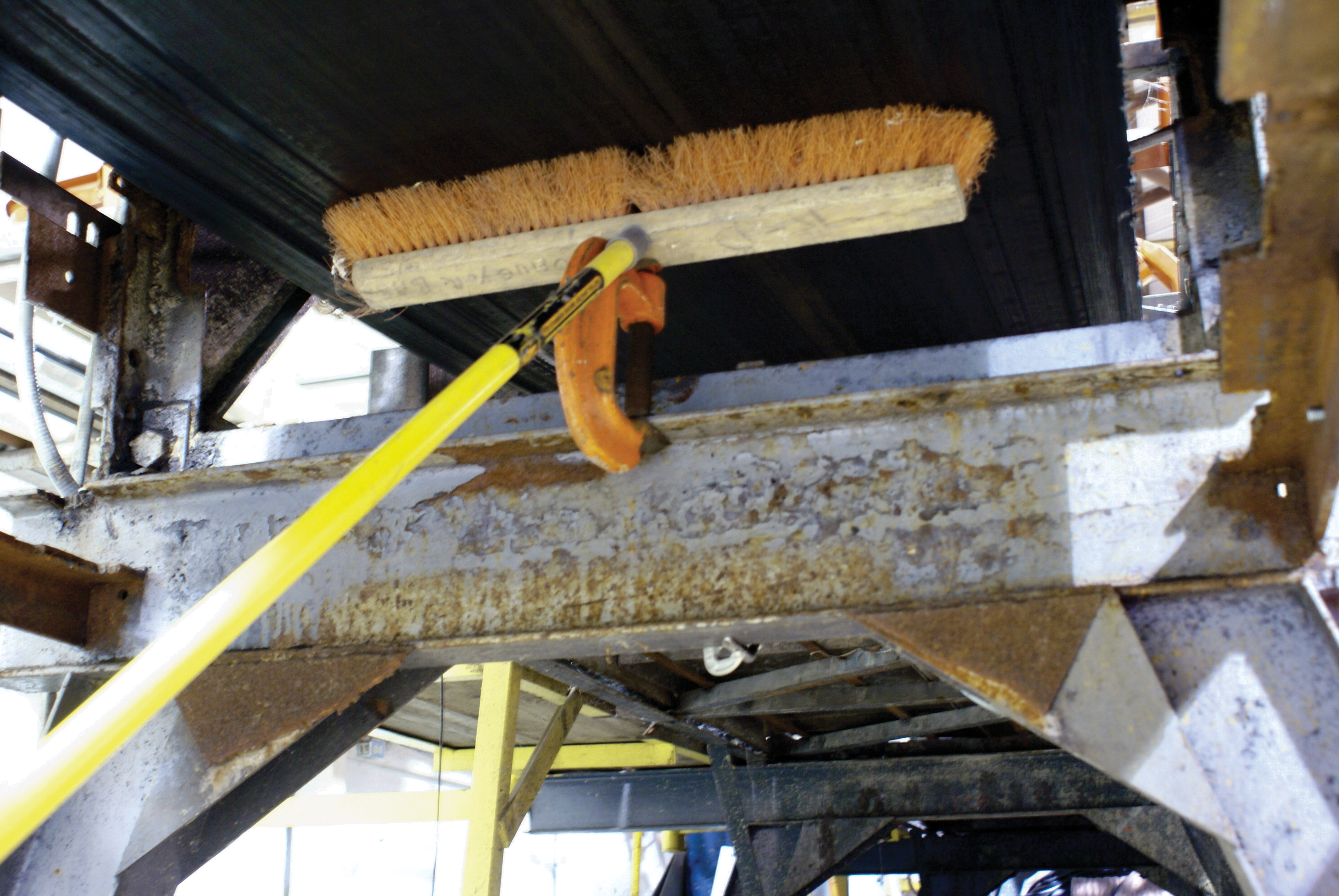
Engineered cleaning systems are designed to reduce space requirements by enabling the cleaner to be installed in the discharge chute. By simplifying blade replacement, maintenance time and labor requirements are minimized. By incorporating advanced materials such as plastics, ceramics, and tungsten carbide, service-life of the blade is extended further, reducing maintenance requirements. By engineering the blade’s edge and improving the tensioning devices that hold the cleaning edge against the belt, cleaning performance is enhanced. Through the use of engineered cleaning systems, the adhesive mass of fines and moisture traveling on the return side of the belt can be almost completely removed.
Monitoring Cleaner Performance
The ability to measure carryback allows for the development of a belt-cleaning performance specification for a given material-handling facility and bulk material. A complete specification will detail the performance required in terms of the average carryback for the facility. The supplier must be required to design, supply, install, commission, and maintain the belt-cleaning system, guaranteeing average carryback levels are not exceeded.
After the belt-cleaning system is installed, carryback tests should be conducted to assess the performance of the belt-cleaning system. An ongoing testing and recordkeeping program will yield information on periodic maintenance requirements an provide payback data for cleaning system maintenance and upgrade opportunities.
By monitoring belt-cleaning performance through carryback testing, the facility can assess the savings of possibly upgrading to more efficient cleaning systems.
Multiple belt cleaner systems take into consideration the dynamics of the surface of the belt and the nature of the material as it passes around the head pulley.
Performance analysis and maintenance programs, implemented by in-house departments, are seldom seen as a priority, due to the overwhelming challenges otherwise presented to the facility. The easiest way to get results from an investment in belt-cleaning equipment is by awarding a service contract to a specialist in the supply, installation, maintenance, and analysis of belt-cleaning systems.
Designing Conveyors for Effective Cleaning
When considering the construction of new conveyors, it is desirable to include the design requirements a specification for belt-cleaner performance. This specification should include an allowance for the amount of carryback measured in grams per square meter (oz/ft2) passing the cleaning system. Plant owners should demand, and engineers should design, conveyor systems with adequate cleaner systems to ensure carryback is maintained below the level specified in the contract. It would encourage the conveyor system designer to include adequate space for installation and maintenance of the belt-cleaning system and to include components on the conveyor that are compatible with the goal of effective belt cleaning.
A common problem in the employment of belt-cleaning devices occurs when insufficient space is provided in the design of the head frame and housing for an adequate multiple belt-cleaner system. This commonly occurs because conveyor engineers have not taken into account the true nature of the conveyed material, particularly when it is in its worst condition. Conveyor engineers should design for clearance and access according to the Conveyor Equipment Manufacturer’s Association (CEMA) recommendations, and the design should allow the belt-cleaner manufacturer to fit and mount the appropriate system, including cutting the holes in the chute after erection and belt installation.
A key to effective belt cleaning is mating the blade to the belt. It stands to reason that the better the blade matches the belt profile, the better it will clean. Anything making it more difficult for the blade to stay in contact with the belt as it moves past the belt cleaner must be avoided in the design of a conveyor system. These undesirable factors include wing pulleys, out-of-round pulleys, and poorly-selected or poorly-installed lagging. Any pulsation or vibration of the belt’s surface lowers cleaning efficiency and adversely affects the life of the belt.
Vulcanized splices are the preferred method of splicing the belt in order to provide optimal performance of the belt cleaning system. Improperly installed mechanical fasteners can catch on belt cleaners and cause them to jump and vibrate or “chatter.” Mechanical splices should always be recessed according to the manufacturer’s recommendations in order to avoid unnecessary damage to the cleaner and the splice.
After installing a belt cleaner, periodic inspection, adjustment, and maintenance are required to maintain effective performance. Just as cleaners must be designed for durability and simple maintenance, conveyors themselves must be designed to enable easy service, including required clearances for access.
Leave Comment