How To Troubleshoot Belt Cleaners
Addressing Common Issues and Enhancing Efficiency
If a cleaning system is performing poorly, despite the blades showing no excessive wear and the tensioner being correctly set, several other potential issues may be at play:
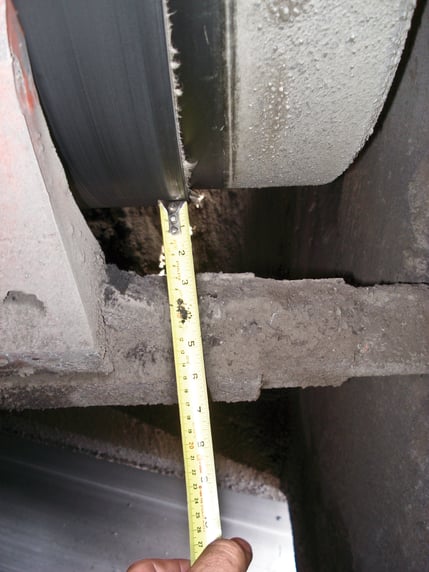
-
The support frame is not parallel to the pulley
-
The cleaner is not installed the proper distance from the belt surface
-
The pressure applied to the cleaner is changing the belt line
-
The blades are not centered on the belt
Addressing any of these factors is crucial for optimizing the cleaning system's performance. Operators should consult the cleaner’s installation manual to identify and implement the necessary corrective actions.
Addressing Belt Flap and Pre-Cleaner "Heeling"
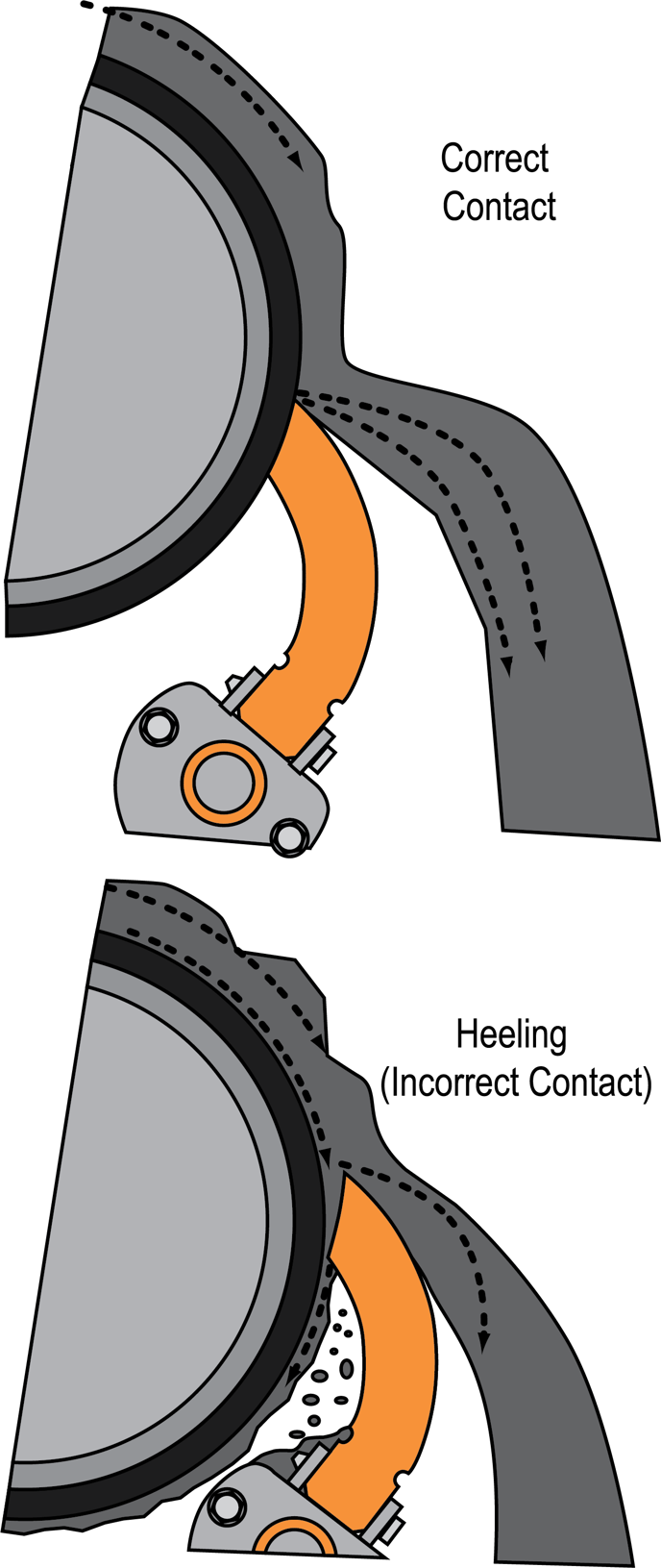
Belt Flap Concerns: Belt flap, characterized by oscillations typically on the return side of the conveyor, can reach amplitudes as high as 25 millimeters (1 inch). This movement can damage belt cleaners, shorten return idler bearing life, and hinder blade contact with the belt, thereby reducing cleaning effectiveness. Techniques to mitigate belt flap include adjusting return idler spacing or using hold-down rollers to stabilize the belt.
Pre-Cleaner "Heeling" Issue: Pre-cleaners are designed to ensure the blade tip contacts the belt first, with the primary cleaner rotating into the belt as the tip wears. However, problems arise if an elastomer blade is mounted too close to the belt, causing the heel of the blade tip to contact the belt first. This gap allows material to accumulate, forcing the blade away from the belt and increasing wear on both the blade and the belt. To remedy this, it is crucial to maintain the correct installation distance so that the leading edge of the blade makes initial contact with the belt, ensuring efficient cleaning.
By addressing these challenges, conveyor operators can enhance the longevity and effectiveness of their belt cleaning systems, reducing maintenance costs and optimizing conveyor performance.