How Notching The Conveyor Belt Ensures Splice Durability
Best Practices and Innovations
To ensure durability at the belt splice, it is beneficial to notch or chamfer the corners of the belt where it joins. This technique, particularly crucial for one-directional belts, involves notching only the trailing end of the belt. Notching is performed at a 60-degree angle from the first fastener on each end of the splice to the belt's edge. This practice prevents the belt corners from catching on the conveyor structure, thereby reducing the risk of splice damage or belt tearing.
Belt Cleaners with Mechanical Fasteners
Mechanical belt fasteners can sometimes conflict with aggressive belt-cleaning systems, especially those using hardened metal blades. To mitigate wear or damage risks to the splice, many operators opt for non-metallic belt cleaner blades (e.g., urethane) when using mechanical splices. Issues in belt-cleaning systems often stem from improper selection or installation of mechanical splices.
Recent advancements have made mechanical fasteners more compatible with belt cleaners. Tools for skiving have been developed, allowing the removal of a uniform strip of belt cover material swiftly and safely. This leaves a smooth, flat-bottomed trough with a rounded lip to receive the splice, replacing older, slower methods involving knives or grinders.
Another innovation includes new designs for "fastener friendly" cleaners. These cleaners feature special blade shapes, materials, and mounting methods to minimize impact problems with fastener plates. For instance, the introduction of "scalloped" mechanical clips allows belt cleaner blades to ramp over the plates without damaging the cleaner or splice, thereby enhancing durability.
Advantages of Mechanical Splices
Mechanical splicing offers several advantages, including easy belt separation for extensions or adjustments in applications like mining. It facilitates simpler servicing of other conveyor components such as pulley lagging, idlers, or impact cradles.
Additionally, mechanical splices reduce repair downtime significantly. Installation typically takes only one to two hours by plant maintenance personnel using basic tools or portable machines, compared to the lengthy process of vulcanization, which requires specialized equipment and contractors. Moreover, mechanical splices are cost-effective, consuming minimal belting material and costing substantially less than vulcanized joints.
Mechanical splices are straightforward to perform and inspect, providing early warnings of potential failures when regularly monitored. They are also suitable for long-term storage, offering flexibility in installation and belt adjustments.
Considerations and Challenges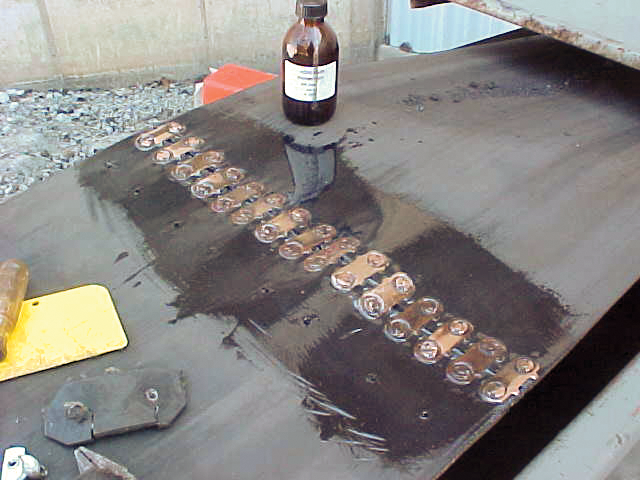
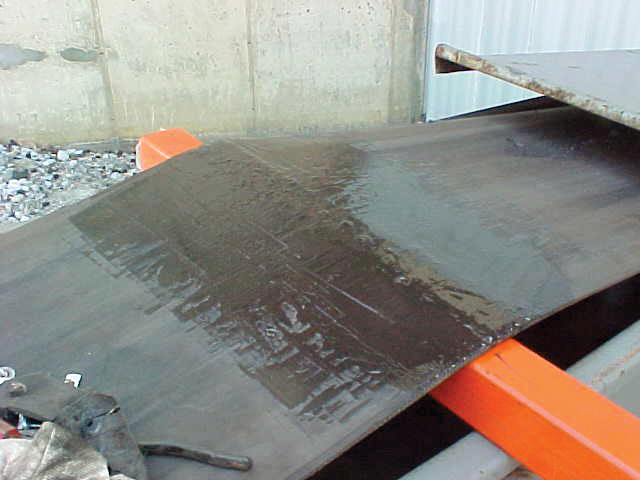
However, mechanical splices have drawbacks. They may not be suitable for conveying hot materials due to heat transmission through metal fasteners, which can weaken belt fibers and lead to fastener failure. Improper inspection and maintenance of fasteners can also result in severe belt damage, including longitudinal ripping if fasteners pull out. Issues such as oversized splices or extended rivets catching on components like skirtboard-sealing systems or belt cleaners can further shorten splice life.
Safe and Efficient Splice Design
Both mechanical and vulcanized splices must be designed with safety factors to withstand expected belt tensions. Manufacturers provide selection tables for mechanical fasteners, while vulcanized splices for high-tension belts are often custom-designed to ensure safety and performance.
Maintenance and Inspection Protocols
A dedicated belt-splicing station equipped with tools and workspace facilitates efficient splice maintenance and installation along the conveyor. Proper tightening of bolt-style fasteners is critical to prevent damage to belt plies. Regular inspection, typically on a weekly basis, ensures early detection of worn fasteners or potential issues like crosswise breaks.
Splice Monitoring 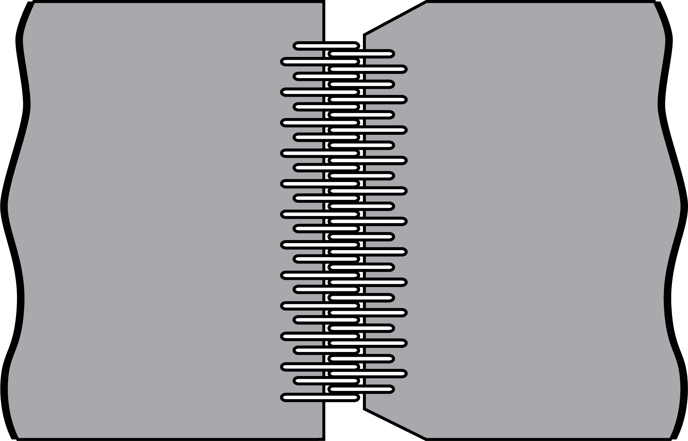
New technologies now enable remote monitoring of splices by measuring elongation, which indicates potential failures. Magnetic targets placed in the belting allow monitoring systems to track splice integrity, promptly alerting operators to any deviations that could lead to downtime or damage.
The Importance of The Splice
Whether employing mechanical fasteners or vulcanized splices, the correct selection, application, and maintenance of a splice are paramount to a conveyor belt's operational success. Neglecting proper splice practices can compromise belt life and operational efficiency. Therefore, adherence to manufacturer recommendations and diligent maintenance practices are essential for maximizing conveyor belt performance and minimizing downtime. As the saying goes, "If you don’t have time to do it right, when will you find time to do it over?"