5 Tips For Proper Conveyor Belt Storage
Proper Storage and Handling of Conveyor Belts: Guidelines to Ensure Optimal Performance and Longevity
The conveyor belt has long been the most economical and efficient method for bulk-material handling in many industries. However, to ensure it performs as expected, the belt must be carefully stored and handled from its manufacture to its installation on the conveyor system.
Improper storage techniques can damage the belt, resulting in poor performance when installed. The importance of following correct procedures increases with the length of storage time and the size of the roll. The costs for handling, shipping, and storing the conveyor belt are minor compared to the purchase price, so proper procedures should be followed to protect this investment. Here are the key storage and handling guidelines:
Rolled on a Core
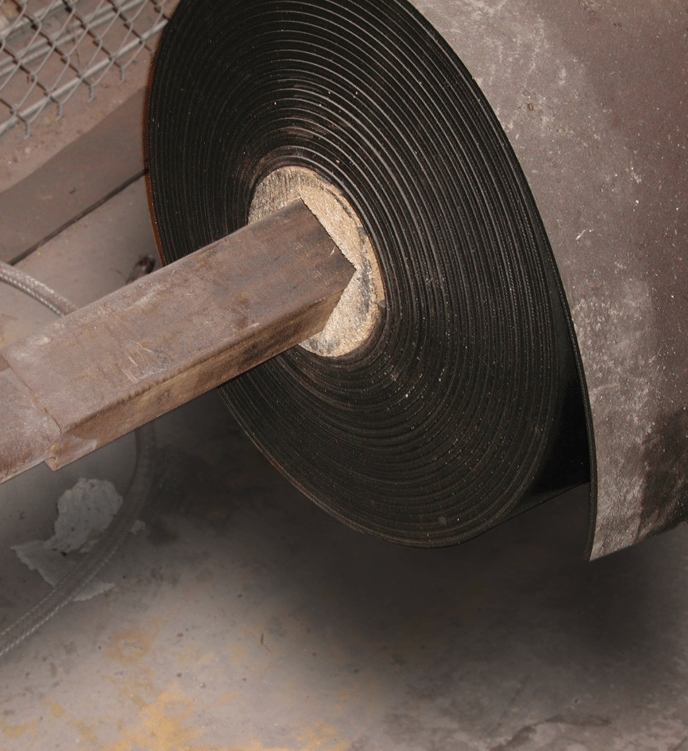
As the belt leaves the manufacturer or supplier, it should be rolled with the carrying side out on a core with a square opening. The core protects the belt from being rolled into a diameter that is too small and provides a means for lifting and unrolling the belt onto the conveyor. The core size is determined by the manufacturer based on the type, width, and length of the belt roll. It can be smaller than the belt’s minimum pulley diameter since the rolled belt is not under tension. The lifting bar should be square to match the core's square opening closely.
Properly Supported
The conveyor belt should never be stored on the ground. Ground storage concentrates the roll's weight on the bottom surface, compressing the belt carcass unevenly. This can stretch the carcass more on one side, causing belt camber, a banana-like curvature running the belt's length.
Under no circumstances should a roll of belting be stored on its side, as this may cause the belt to expand unevenly, creating camber problems. Moisture may also migrate into the carcass through the cut edge, leading to carcass issues or belt camber.
The belt should be supported in an upright position on a stand, off the ground. This distributes the stress of half the roll’s weight on the core, relieving the load on the bottom. This support stand can be used during shipping to distribute the belt's weight better and later in the plant for storage, or the belt can be transferred to an in-plant storage system that properly supports the roll. Proper support from manufacture to installation is crucial.
Rotated on Its Stand
If the support stand is designed correctly, the roll of the belt can be rotated every 90 days. This more evenly distributes the load throughout the carcass. The reel of belting should be marked at the factory with an arrow indicating the direction of rotation. Rotating the belt in the opposite direction will cause the roll to loosen and telescope.
Properly Protected
During shipping and storage, the roll of the belt should be covered with a tarp or wrapped in opaque, water-resistant material to protect it from rain, sunlight, or ozone. The covering should remain in place throughout the storage process.
The belt roll should be stored inside a building to protect it from the environment. The storage area should not contain large transformers or high-voltage lines that may create ozone and affect the belt. The building does not need to be heated but should be relatively weather-tight.
Lifted Correctly
When lifting a roll of the belt, a square lifting bar of the correct size should be placed through the core. Slings or chains suitable for the roll's weight should be used, and a spreader bar should be utilized to prevent the chains or slings from damaging the belt edges.
Additional guidelines can be found in ISO 5285. Belt manufacturers can provide specific guidance for their products.