Basics of Conveyor Belt Vulcanization
Conveyor Belt Splice Integrity and Performance
Vulcanization is the process of curing raw rubber by combining it with additives under heat and pressure ("hot" vulcanization). In the belting trade, bonding belt ends with adhesives is known as "cold" vulcanization.
Vulcanization is generally preferred for belt splicing due to its superior strength, longer service life, and cleaner operation. It's indispensable for high-tension steel-cord belting, providing maximum belt tension and excellent pulley-to-belt traction. Unlike mechanical splices, vulcanized splices rely solely on rubber adhesion to the carcass or steel cords, achieved through intermediary materials like tie gum or installation gum.
Steps in Vulcanizing a Belt
The process of vulcanizing a belt involves several steps:
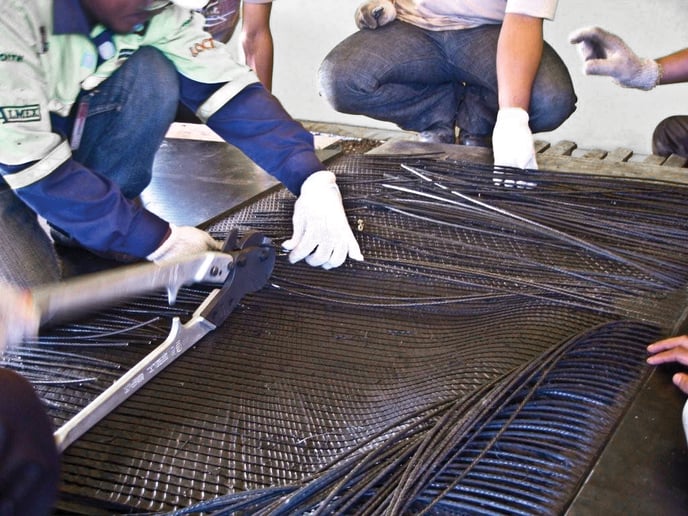
-
Preparation of the Belt Ends: For fabric carcass belts, the ends are cut at the correct angle and then stripped to expose the plies. Steel-cable belts involve cutting back the rubber cover.
-
Application of Intermediary Material: Layers are built up with bonding agents, creating a sandwich-like structure. For steel-cable belts, cords are overlapped, and bonding agents are applied before adding fill and cover rubbers.
-
Curing of the Splice: The assembled materials are pressed and cured using heat, pressure, and/or time to form the final splice. This process ensures a high-strength joint suitable for demanding applications.
Splice Patterns
Vulcanized splices require removing layers of rubber covers and fabric carcass to overlap and join belt ends. Generally, the splice geometry remains consistent whether it's hot or cold vulcanized.
Bias splices are the most common, featuring an angled cut that increases the bonding surface length and reduces stress as the belt wraps around pulleys. This 22-degree bias angle also minimizes the risk of the splice tearing open at its leading edge, a critical benefit.
Another splice gaining popularity, especially with high-tension fabric belts, is the finger splice. This design involves cutting belt ends into narrow triangular "fingers" typically 30 or 50 millimeters wide at the base and between 850 to 1200 millimeters long, depending on belt specifications. The fingers are interlaced and then subjected to hot vulcanization in a single operation.
Types of Vulcanization
There are two types of vulcanization:
-
Hot Vulcanization: Involves overlapping belt layers with glue and rubber, then curing them in a heated press. This method requires specialized equipment and attention to time, temperature, and pressure.
-
Cold Vulcanization (Chemical Bonding): Joins belt layers using adhesives that cure at room temperature. Although it requires longer curing times, it's advantageous in remote locations or where power sources are limited.
Advantages of Vulcanization
Vulcanized splices offer significant advantages:
- They provide a strong, seamless joint capable of withstanding high belt tensions.
- They prevent material sifting through the splice, making them ideal for controlling fugitive material.
- They do not interfere with rubber skirting, idler rolls, or belt cleaners.
Disadvantages of Vulcanized Splices
Despite their benefits, vulcanized splices have drawbacks:
- They are more expensive and time-consuming to perform compared to mechanical splices.
- The preparation process can be complex, requiring significant downtime for curing.
- Emergency repairs involving vulcanized splices can lead to extended downtime and higher costs.
Considerations for Belt Design and Maintenance
When designing conveyor systems with vulcanized belts, it's crucial to plan for belt adjustments using a take-up pulley mechanism. This reduces the need for frequent splicing due to belt stretch, thereby optimizing operational efficiency and minimizing downtime.
While vulcanized splices require careful planning and investment, they offer unparalleled reliability and performance in conveyor belt applications. Properly executed, they ensure long-term operational success and minimize maintenance disruptions. For detailed guidance on vulcanization techniques and materials, consulting the belting manufacturer is recommended. This approach ensures adherence to best practices and maximizes the lifespan of conveyor belts in various industrial settings.