All About Primary, Secondary, & Tertiary Belt Cleaning Systems
Key Design Considerations
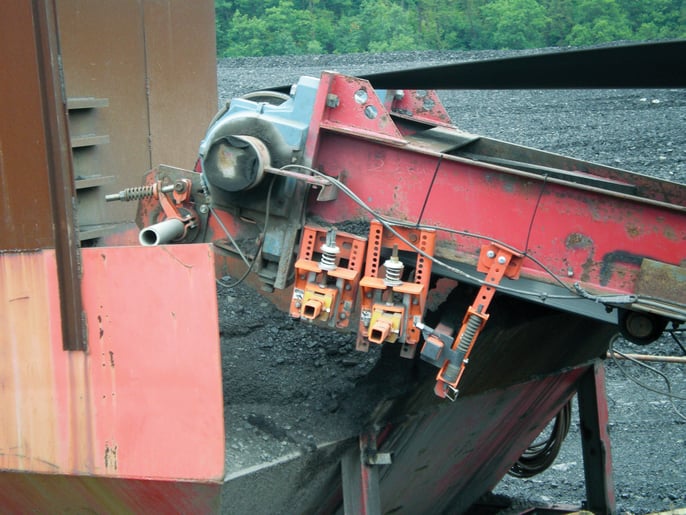
In General
Designing conveyor belt cleaning systems to address "worst-case" material conditions, rather than "normal" operating conditions, is crucial. This approach ensures that the cleaning systems can effectively adapt to material variations, maintaining optimal performance even under challenging circumstances. The positioning of belt cleaners should be as close to the material discharge point as possible. This strategic placement supports the cleaning elements against a solid surface, enhancing their effectiveness in removing debris and maintaining a clean belt surface. Belt cleaners must be installed outside the material trajectory to prevent cleaned materials from building up on the blades and structures. Each head pulley should be equipped with a belt cleaning system that includes, at a minimum, a primary cleaner and a secondary cleaner, with provisions for adding tertiary cleaners if necessary. The design of these cleaning systems should facilitate simple maintenance and blade-replacement procedures. Regular maintenance, as recommended by manufacturers, is essential to keep the belt cleaners operating at peak performance.
Primary Cleaners
Primary cleaners are responsible for the initial rough cleaning of the conveyor belt. They should be designed with flexible elastomer blades and radial-adjustment tensioning devices to ensure efficient cleaning. These cleaners should be installed on the face of the head pulley, just below the material trajectory, utilizing a positive-rake cleaning angle. The blades of primary cleaners should maintain a constant-cleaning angle and area design to maximize their effectiveness. Pre-cleaners, which fall under the category of primary cleaners, should be designed for use on both one-directional and reversing belts. For reversing belts, a pre-cleaner should be installed on each discharge pulley to ensure comprehensive cleaning coverage.
Secondary Cleaners
Secondary cleaners play a critical role in removing the majority of the material that passes by the pre-cleaner's blades. These blades should contact the belt just past the point where the belt has left the head pulley. Alternatively, secondary cleaners can be positioned behind the head pulley with a hold-down roll above the blades. This hold-down roll should have a minimum diameter of 100 millimeters (4 inches) to ensure effective cleaning. The blades of secondary cleaners should be designed to contact the belt in a negative-rake position and be constructed of tungsten carbide or similar abrasion-resistant materials for durability. For one-directional belts, the cleaners should be adjusted using a radial adjustment tensioning device. On reversing belts, a vertical-spring tensioner should be used. Reversing belts should have a reversing secondary cleaner installed as close as possible to each terminal (discharge) pulley to ensure thorough cleaning.
Tertiary Cleaners
The design of conveyor load zones should account for the possible addition of tertiary cleaners. These cleaners provide an additional layer of cleaning and should utilize a separate dribble chute or scavenger conveyor to return the carryback to the main material flow. By planning space for tertiary cleaners, the overall efficiency and cleanliness of the conveyor system can be significantly enhanced. Other Considerations To support the effective operation of belt-cleaner installations, necessary utilities such as water, electricity, and compressed air should be readily available at convenient points. Additionally, the design of the conveyor system should provide clearances and access in accordance with CEMA recommendations. This ensures that maintenance and adjustments can be carried out efficiently, maintaining the overall performance and longevity of the belt cleaning systems.