Why Traditional Conveyor Belt Cleaning Can Fall Short
Understanding common failures and how to improve belt cleaning efficiency
Conveyor belts are a crucial component in many industries, ensuring smooth material transport and operational efficiency. However, traditional belt cleaning methods can fall short, leading to inefficiencies, material loss, and potential safety hazards. Understanding why these methods fail can help industries improve their cleaning strategies and optimize performance.
Improper Installation and Maintenance
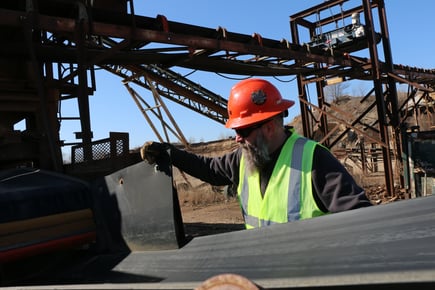
One of the primary reasons belt cleaners fail is improper installation or lack of maintenance.
If a belt cleaner is not installed correctly, it may not make sufficient contact with the belt, significantly reducing its cleaning effectiveness—sometimes by as much as 40–50%. Incorrect positioning, insufficient tensioning, or misalignment can lead to uneven wear and ineffective cleaning.
Regular maintenance is also essential, as wear and tear can lead to decreased efficiency over time. Blades wear down, tension can loosen, and buildup of material on the cleaner itself can cause performance issues. Routine inspections and proactive adjustments can ensure optimal performance and prevent costly downtime.
Incorrect Cleaner Selection
Choosing the wrong belt cleaner is another major issue. The diameter of the pulley plays a significant role in selecting the appropriate cleaner, yet many operations use undersized cleaners. When a belt cleaner is too small for the pulley, it will not perform effectively, leading to increased material carryback and potential equipment damage.
Additionally, different applications require specific cleaner types. For example, polyurethane blades may work well for certain materials, while tungsten carbide blades may be required for tougher applications. Failing to match the cleaner type to the material and operating conditions can result in suboptimal performance and frequent replacements.
Challenges with Belt Condition and Splicing
Belts with poor surface conditions, cleats, or weak splices can severely impact cleaning efficiency. Surface damage allows material to settle into crevices, making it difficult for traditional cleaners to remove carryback. If a belt has tears, gouges, or an uneven surface, the cleaner may not make sufficient contact, reducing its ability to remove debris effectively.
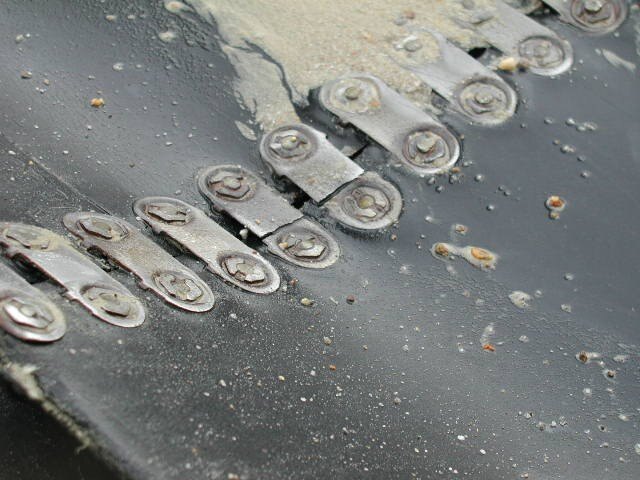
Similarly, improper splicing techniques—such as the use of unskived mechanical clips—can
disrupt the function of belt cleaners. A properly skived splice provides a smooth transition that allows cleaners to work more effectively. Without proper attention to splicing, belt cleaners may
experience premature wear, reduced effectiveness, and potential damage to both the cleaner and the belt itself.
Difficult Material Characteristics
Certain materials pose significant challenges to traditional belt cleaning systems. Extremely sticky or wet fines tend to adhere to the belt, making them difficult to remove with standard cleaners. High-moisture content can cause material to clump and stick, reducing the effectiveness of scraper blades and increasing the likelihood of buildup on rollers and pulleys.
As material characteristics change, traditional cleaners may struggle to maintain effective cleaning, leading to increased carryback and operational issues. In industries handling materials such as clay, coal, or biomass, alternative or supplementary cleaning methods, such as secondary scrapers, air knives, or wash systems, may be required to achieve satisfactory results.
Inconsistent Carryback Standards
Traditional belt cleaning methods are designed to remove approximately 90% of material carryback. However, in situations where higher cleanliness is required—such as in environmentally sensitive locations, over roadways, or near waterways—this level of performance may not be sufficient.
Some operations have stricter regulatory or safety requirements that demand more efficient cleaning solutions. Excessive carryback can lead to material loss, safety hazards, environmental concerns, and increased cleanup costs. In these cases, additional or more advanced belt cleaning systems, such as multiple-stage cleaners or specialized blade materials, may be necessary to meet stringent performance expectations.
Conclusion
Traditional conveyor belt cleaning methods can be effective but are often prone to failure due to installation errors, improper selection, belt condition, material properties, and varying cleanliness requirements. To optimize conveyor performance, industries must carefully assess their belt cleaning systems, ensure proper installation and maintenance, and consider advanced cleaning technologies when necessary. By addressing these challenges, companies can improve efficiency, reduce material waste, and enhance workplace safety. Investing in the right belt cleaning solutions can lead to long-term operational benefits, reduced downtime, and improved compliance with environmental and safety regulations.