The Truth About Brush Cleaners
Evaluating Brush Cleaners: Benefits, Limitations, and Key Considerations
Brush Cleaners in the Market
Brush cleaners are widely available, produced by major manufacturers, independent competitors, and even crafted in workshops by skilled millwrights. Their widespread presence suggests that they should work effectively. However, while the concept of brush cleaners appears sound, there are several important factors to consider before implementing them in a conveyor belt system. Despite their availability, not all brush cleaners are created equal, and their effectiveness depends largely on design, installation, and maintenance.
What Are Brush Cleaners and How Do They Work?
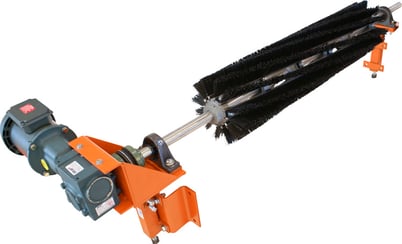
Brush cleaners are belt-cleaning devices designed to remove residual material from conveyor belts. They operate using rotating bristles that come into contact with the belt to dislodge material. Unlike rigid blade scrapers, brush cleaners rely on a softer, more flexible approach to debris removal. They are often powered by a motor, ensuring continuous rotation that allows for constant cleaning. While they offer a non-abrasive cleaning method, their effectiveness depends on various factors, including the type of brush cleaner used, the material being conveyed, and proper maintenance.
Types of Brush Cleaners: Spiral vs. Strip
There are two main types of brush cleaners:
- Spiral Brush Cleaner: This is the most common type, featuring bristles wrapped around a rotating shaft in a spiral pattern, similar to a barber pole. This design ensures continuous contact with the belt surface, which can help in providing more consistent cleaning action. However, the uniformity of cleaning may be compromised if material accumulates unevenly on the belt.
- Strip Brush Cleaner: Unlike the spiral type, the strip brush cleaner consists of multiple bristles arranged in a straight line along a rotating shaft. This style provides direct contact but lacks the continuous engagement of the spiral design, making it more suitable for specific applications where precise debris removal is needed.
Each type has its own advantages, but their fundamental cleaning principle remains the same: brushing material off the conveyor belt. Choosing the right type depends on the application and the nature of the material being handled.
Effectiveness of Brush Cleaners vs. Primary and Secondary Setups
While brush cleaners do remove some material, their efficiency is significantly lower than a traditional primary and secondary scraper setup. Research indicates that a brush cleaner alone achieves a maximum cleaning efficiency of about 40%, whereas a combination of a traditional primary and secondary scraper can achieve 90% efficiency. The primary scraper removes the bulk of the material, while the secondary scraper deals with finer residues.
A single brush cleaner is unlikely to achieve the same level of cleanliness. Even adding multiple brush cleaners may not be sufficient to reach the effectiveness of a well-maintained primary and secondary scraper system. Consequently, while brush cleaners can complement a belt cleaning system, they should not be relied upon as the sole cleaning mechanism, especially for applications that require high cleanliness standards.
The Risk of Over-Tensioning
A common issue with brush cleaners is the tendency to apply excessive tension. Maintenance teams often believe that increased pressure will enhance performance—similar to pressing harder while sweeping a floor. However, over-tensioning can cause bristles to deflect beyond their design limit (typically around a quarter of an inch). This leads to bristle breakage, reducing effectiveness and increasing maintenance costs. Additionally, excessive tension can result in unnecessary motor strain, increasing power consumption and reducing the lifespan of the brush cleaner components.
Over-tensioning also accelerates wear, making the brush cleaner less reliable over time. It can lead to uneven cleaning, where some sections of the brush wear out faster than others, diminishing overall efficiency. Proper tensioning, in accordance with manufacturer recommendations, is essential to achieving optimal performance and longevity.
Brush Cleaners and Dust Problems
One often overlooked drawback of brush cleaners is their potential to increase dust issues. The spinning motion of the brush generates induced air, which can disturb settled material and create airborne dust. This occurs because the rotating bristles pull air into the system, potentially redistributing fine particles into the surrounding environment.
If dust control measures are not in place, this can lead to compliance and safety concerns, such as increased health risks for workers and potential environmental violations. Effective dust management strategies, such as the use of dust suppression systems or proper ventilation, are crucial when using brush cleaners, as they contribute to air movement in the system. Additionally, regularly cleaning and maintaining the brush cleaner itself can prevent material buildup, which can exacerbate dust-related problems.
Final Thoughts
Brush cleaners may seem like a simple and effective solution for conveyor belt cleaning, but they come with limitations. Their lower efficiency compared to scraper systems, risk of over-tensioning, and potential to create dust must be carefully considered. While they can be a useful addition to a belt cleaning setup, they should not be relied upon as a sole cleaning method. Proper installation, maintenance, and dust control strategies are essential to maximize their benefits and minimize unintended consequences. Understanding the strengths and weaknesses of brush cleaners can help operators make informed decisions about their use in different conveyor belt applications.