Selecting The Right Belt Cleaner for Your Application
Selecting the Right Belt Cleaner: A Comprehensive Guide
Specification Must-Haves
In order for your belt cleaners to effectively remove carryback, they must be well-suited to their application. Choosing the right belt cleaner requires assessment of several different factors. Belt speed, belt width, head pulley diameter, material type, material path width, types and quantitiy of splices, and application temperature all influence which cleaner will be the most effective.
Belt cleaners are not one-size-fits-all.
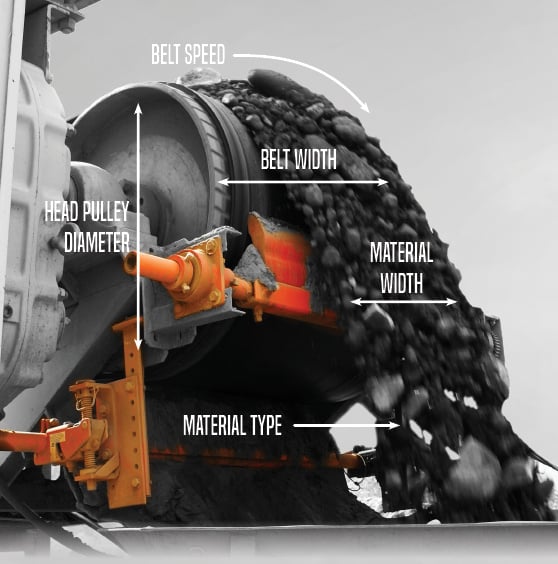
Belt Speed
Each belt cleaner is unique. This means that every belt cleaner and every mainframe is designed and manufactured with a variable amount of strength.
Faster belts require stronger mainframes.
When a conveyor system’s belt speed exceeds the maximum range of a belt cleaner, it can cause the cleaner to vibrate, deflect, and possibly bend the mainframe. Correctly matching the belt speed of the conveyor to an appropriate belt cleaner is crucial to ensuring proper blade-to-belt contact and maintaining optimal cleaning performance.
Belt Width
Knowing both the width of the belt and the troughing angle helps to accurately specify the blade width appropriate for the material path.
- Blades for flat belts should be 2 inches less belt width
- Blades for belts with a 20° trough angle should be 4 inches less belt width
- Blades for belts with a 35° trough angle should be 6 inches less belt width
- Blades for belts with a 45° trough angle should be 8 inches less belt width
Ideally given the above information, the width of the belt cleaner should match the width of the material path at the point of discharge from the belt. This ensures even wear and reduces carryback and material buildup.
Head Pulley Diameter
Correctly matching a belt cleaner to the specifications of the conveyor system ensures that the engineered blade design maintains consistent surface area contact with the face of the belt along the radius of the pulley.
If the belt cleaner is not properly sized to the head pulley of the conveyor it will not maintain the proper angle of attack and surface area contact, resulting in poor cleaning performance and reduced wear life.
Larger head pulleys require larger belt cleaners and blades to properly match their radius while smaller head pulleys require smaller belt cleaners and blades to properly match their radius.
Material Path Width
If the blade width does not closely match that of the material width, cleaning results will be less than desired. Oftentimes when this is the case, you will end up with a “smiling” blade. This is where the middle of the blade undergoes more wear than the outer edges, leading to uneven erosion of the cleaner.
Matching the width of the blade to the width of the material path ensures that the urethane wears evenly, maintaining optimum blade-to-belt contact. With solid contact between the blade and the belt, material can be reliably removed from the belt over the life of the cleaner.
Material Type
Whether the material you run is dry, muddy, or anywhere in between it is important to base your belt cleaner selection on your operation’s material type. Factors like material temperature, moisture, and chemical composition all influence which urethane is needed to keep your blades operating at maximum efficiency.
Be mindful of changes in material characteristics due to changes in the material source or environment.
Specially engineered urethane formulations provide optimal cleaning performance and maximum wear life over different applications. Matching the right type of urethane blade to the application ensures optimal cleaning performance and maximum wear life by avoiding unusual or premature wear and damage to the blade.
Application Temperature
Urethane blades are formulated to handle certain operating temperatures. Matching the appropriate urethane blade to the conveyor system’s operating temperature helps ensure optimal cleaning performance and maximum wear life.
Applications that exceed the blade’s acceptable temperature range will suffer unusual wear as the urethane melts under excessive temperatures, leading to poor cleaning performance, premature wear, and shortened blade life.
Splices
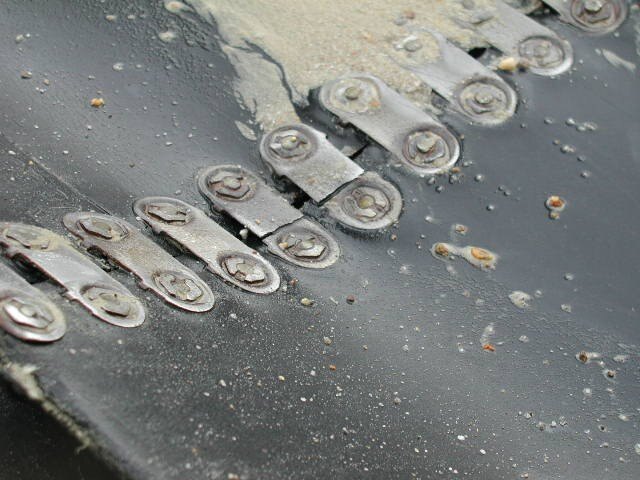
Types of splices play a part in belt cleaner performance and in potential damage to the blade. A vulcanized splice is the preferred splicing method as far as belt cleaners are concerned. Vulcanized splices allow the cleaner to maximize cleaning performance as well as extend blade life.
A mechanical splice should be skived or properly dressed to allow for proper cleaning and sealing. If impossible to properly recess a mechanical splice a splice should be dressed by grinding away the high spots or encapsulating the splice to protect both it and the belt cleaner from impact damage. A damaged/gouged blade due to improper mechanical splices/ skiving won’t be able to clean as intended.
Do you need a secondary or tertiary cleaner?
Primary belt cleaners with urethane blades typically remove between 50 and 70 percent of material carryback. In some applications, this reduction in carryback is adequate in maintaining clean, safe, and productive conveyor operations. In other instances, secondary and even tertiary cleaners may be required to adequately and successfully ensure optimal cleaning and operation.
Secondary belt cleaners take into consideration the changing dynamics of the belt surface as it rounds the head pulley. Any material that evades the primary cleaner blade will then encounter the secondary, further eliminating carryback issues. Secondary cleaners are specially designed and engineered to provide additional cleaning past the point of discharge to increase overall belt cleaning performance. They run at a different angle compared to a primary cleaner which makes them unsuitable on belts that experience reversing or roll back.
When only water or small particles remain, a tertiary can be used to finish the job. These are installed past the snub pulley, outside of the discharge chute allowing for easy return of material to the main material flow.
The addition of secondary and tertiary cleaners can provide as much as 90 to 95 percent of carryback removal.
Belt cleaner selection checklist
What is the speed of the belt? | |
What is the width of the belt? | |
What is the diameter of the head pulley? | |
What type of material are you conveying? | |
What is the width of the material path? | |
What is temperature of the application? | |
How many splices are on the belt? | |
What kind of splices are present? |
* Each of these factors are essential in choosing the right belt cleaner for your application. Have
these values ready when you contact your Martin Engineering representative.