Long-Lasting Effectiveness of Dust Suppression Systems
Enhancing Conveyor Dust Control with Residual Chemical Solutions
A well-designed residual suppression system enables effective control of fugitive dust across expansive areas by strategically applying the solution at key points.
Residual Chemical Suppression Agents Surfactants dampen dust fines, causing particles to clump together and preventing them from becoming airborne. However, once the solution evaporates, the effectiveness of standard surfactants diminishes. In many scenarios, dust suppression is necessary not only during material movement through various transfer points but also after materials have been stored in bins, railcars, barges, or stockpiles. In such cases, employing a water/surfactant spray or foam system with a longer-lasting residual effect is advisable. Residual dust suppression proves beneficial for:
- Large areas with multiple application points
- Long distances between application points
- Stackers or trippers
- Crushers or mills
- Elevated transfer points where applying dust suppression is challenging
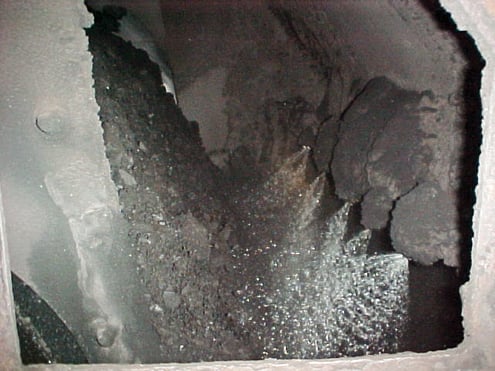
A well-designed residual suppression system allows for comprehensive control of fugitive dust over a wide area by applying the solution strategically. In contrast, using water and/or fog systems for large areas necessitates multiple application points, multiple pump stations, longer water, chemical, and air lines, increased pumping capacity, and more application nozzles—all factors that can significantly escalate costs and, in some cases, reduce effectiveness.
Coal transported from unloaders to open storage piles often remains there for extended periods. Material stored in open stockpiles is exposed to varying climates, including wind, sun, and precipitation.
The sun's heat can evaporate moisture from stored material, increasing its susceptibility to wind erosion. Wind erosion generates substantial dust that settles on nearby homes and yards. When coal is reclaimed from storage, it may be dry, posing greater dusting challenges than during initial handling. Dusty materials like calcined coke or iron-ore pellets may require dust control from production to end use, spanning several weeks and thousands of kilometers (miles). In such cases, applying a residual surfactant/binder to materials may be more economical than using surfactants and water at multiple sites throughout the materials-handling system. Various residual binders are available for this purpose.
Longer-Lasting Effects
The goal of a residual suppressant, or binder, is to aggregate fines into larger particles or to each other, maintaining their structure even after moisture evaporation. In some instances, hygroscopic materials such as calcium chloride are employed to slow moisture evaporation from treated materials. This approach can offer cost-effective treatment. Common binders include lignin, tannin, pitch, polymers, and resins. Combined with surfactants for enhanced wetting, these compounds coat larger particles and act as an adhesive to attract and retain dust fines.
Application of residual binders tends to be costlier than surfactant applications due to the need for higher concentrations. Binders are typically applied at dilution rates ranging from 50-to-1 to 200-to-1 (2.0 percent to 0.5 percent), despite being less costly per kilogram (pound).
It's important to note that using a residual chemical can reduce the number of application points required at a plant, thereby lowering maintenance needs.
When selecting a binder, understanding its impact on transfer equipment and conveyor belts is crucial. A binder that adheres well to materials may also stick to handling equipment. Proper application is critical to avoid overspray onto process equipment or empty belts, which can lead to significant production and maintenance issues.
Consideration must also be given to the binder's environmental impact on both the treated material and its surroundings. If a water-soluble binder is applied to material going into a stockpile exposed to rain, parts of it may end up in runoff, posing an environmental risk. Most chemical manufacturers offer only environmentally compatible binders, but this should be discussed with the supplier to ensure alignment.