Minimum Requirements for Conveyor Belt Guarding
Practical Guidelines for Effective Guard Design, Installation, and Maintenance
Conveyor belt guarding plays a critical role in protecting workers from hazardous machinery and ensuring the smooth operation of industrial equipment. However, its effectiveness hinges on thoughtful design, proper installation, and consistent maintenance. Implementing best practices can significantly reduce the risk of workplace injuries and improve overall operational safety.
The following guidelines outline key considerations for creating and maintaining safe, effective guarding systems in compliance with industry standards.
Avoid Creating Hazards
Guards are meant to enhance safety, not introduce new risks. To achieve this, they should be lightweight—ideally weighing less than 50 pounds—to ensure they are manageable during installation, removal, and maintenance. Sharp edges or protrusions must be eliminated to prevent accidental injuries during handling or operation. For hinged guards, careful design is crucial to avoid creating pinch points, which could pose significant risks to workers during normal use or maintenance activities. The guard design should always prioritize both safety and ergonomics, ensuring workers can handle them efficiently and safely.
Prevent Access with the AUTO Principle
The AUTO principle—Around, Under, Through, or Over—provides a clear framework for effective guard design. Guards should be constructed and positioned to completely block workers from accessing hazardous areas. Openings in guards must be carefully sized and positioned based on MSHA and OSHA standards, taking into account the size of a worker's hand or fingers, ensuring even accidental access is impossible. This principle is vital for preventing contact with moving machinery and significantly reducing the risk of severe injuries.
Color Coding for Visibility and Inspection
Effective color-coding plays a dual role in safety and maintenance. Guards should be highly visible, typically painted yellow or orange. Whatever color the guards are painted must not be the same as the machinery behind it. Incorporating black fields with yellow borders adds another layer of visibility, creating a high-contrast pattern that helps guards stand out. This design choice also facilitates quick visual inspections, enabling workers and supervisors to easily spot potential issues with the equipment or guards, such as wear, material buildup, or improper installation.
Maintain Proper Distance
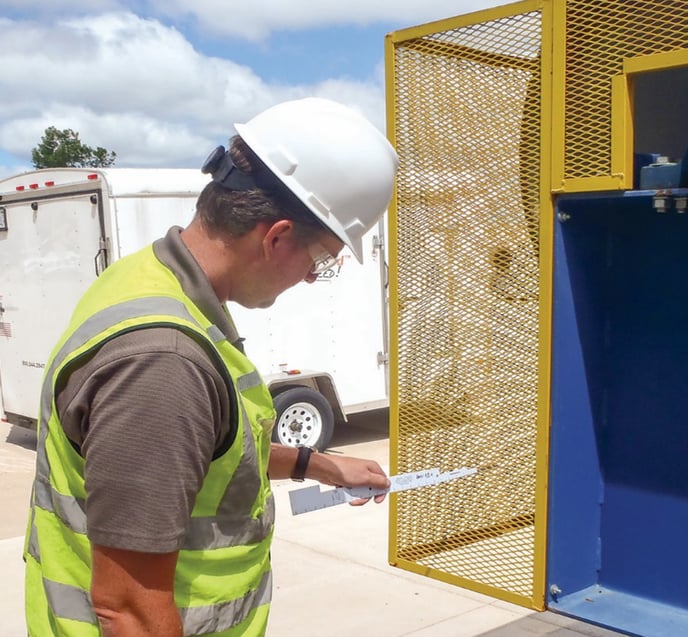
The distance between guards and moving parts is critical for safety. ANSI standards provided detailed guidelines on this, specifying that larger openings in a guard require a greater separation distance from rotating equipment. This ensures that even in the event of accidental contact, workers are protected from harm. Proper distance also accounts for potential tool use during maintenance, minimizing the likelihood of tools being caught in moving parts while maintaining safety for workers.
Secure Fastening
Guards must be securely attached to prevent unauthorized or accidental removal. OSHA regulations require guards to be removable only with tools, ensuring that access is controlled and intentional. MSHA standards emphasize the importance of secure fastening to avoid guards becoming dislodged during operation. While zip ties might seem like a quick and inexpensive solution, they are unsuitable for long-term use because they degrade over time, potentially compromising safety. Instead, use robust fastening systems such as bolts, clamps, or locking mechanisms that meet regulatory requirements and provide long-term reliability.
Routine Inspections and Maintenance
Safety guards are only effective if they are properly maintained. Regular inspections are essential to confirm that guards are securely attached, free of damage, and functioning as intended. Maintenance teams should check for wear, cracks, corrosion, or other issues that could weaken the guard’s integrity. After any service or repair, guards must be reinstalled correctly and securely. Maintenance schedules should incorporate routine guard checks, and any deficiencies should be addressed promptly to ensure ongoing worker safety and compliance with safety standards.
By following these best practices, companies can significantly reduce the risk of accidents and ensure a safe working environment around conveyor belts and other machinery.