Comparing Flat & Troughed Conveyor Belts
Versatility and Practical Applications
Many bulk materials can be transported using flat belts, which are especially suited for materials with a steep angle of repose—a measure of the slope formed by a heap of material. Materials with angles of repose exceeding 30 degrees, such as irregular, stringy, fibrous, and interlocking substances like wood chips and bark, are well-suited for flat belts. Conversely, materials with a low angle of repose require troughed belts to maintain efficient material conveyance due to reduced volume when using flat belts.
Flat belts are particularly effective when there is a need to discharge a load, or part of it, from the belt at intermediate points using plows or deflectors.
Belt feeders predominantly utilize flat belts because of their short length and the operational constraints that make forming them into troughs impractical. These feeders operate under heavy loads with high-tension conditions that pose challenges for belt toughness and sealing. Effective management of these challenges involves maintaining generous edge distances and operating at lower speeds to control spillage. Many feeder belts feature skirtboards and full-length sealing systems. Some employ a dual chutewall design with an inner wear liner and an outer chutewall that includes the belt's edge seal.
Unlike troughed conveyors, flat belts eliminate the need for transition areas and related transition problems. However, other conveyor components and issues discussed elsewhere in this book are still relevant to flat belt conveyors.
Troughed Conveyors
Troughed conveyors, by contrast, offer a significant increase in carrying capacity for most materials and conveyor systems by shaping the belt into a trough.
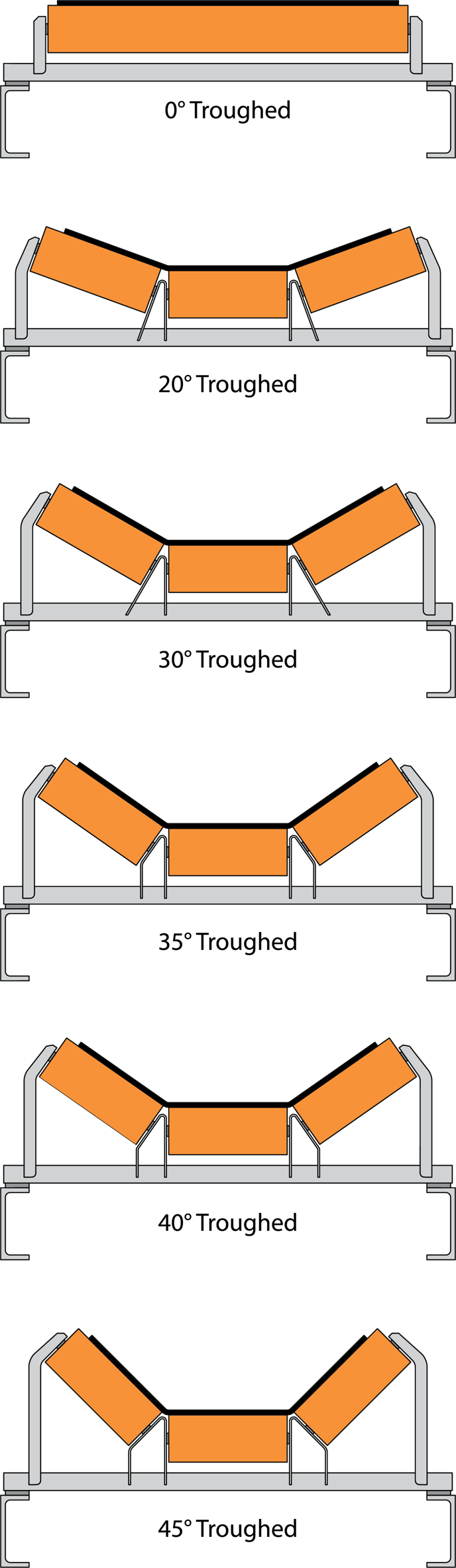
The standard trough angles in Europe are typically 20, 30, and 40 degrees, while in North America, common angles include 20, 35, and 45 degrees. However, due to the global economy, conveyors with various trough angles can now be found worldwide. Previously, the 20-degree trough was standard, but deeper troughs have become more prevalent as advancements in belt design allow for greater flexibility without premature failure.
In specialized applications like high-tonnage mining, 60-degree catenary idlers are used to minimize spillage and impact damage. Longer and higher-speed conveyors often necessitate thick belts, sometimes reinforced with steel cords, which may limit trough capability. The 20-degree trough, with its lower bending requirements and reduced stress on the belt, allows for the use of thicker belts, enabling transportation of heavier materials and larger lumps.
Trough angles greater than 20 degrees are typically chosen for materials with low angles of repose and offer versatility across a wide range of applications. However, higher trough angles require careful consideration of transition distances and exposed edge requirements for skirt sealing.
While troughed belts increase capacity, they also have drawbacks. Longer transition distances are necessary to prevent belt edge stress, and steeper trough angles are more susceptible to wind effects and belt damage.
Troughing the belt generally improves belt tracking and containment of materials by reducing edge spillage and wind losses.
In most cases, the selection of trough angle for a conveyor is determined by the need to use the narrowest and most cost-effective belt capable of transporting the required tonnage of material.