Benefits of Pairing Belt Cleaners With Washbox System
The Evolution and Benefits of Modular Wash-Box Systems
To effectively clean a conveyor belt, one of the most efficient methods involves using both traditional cleaners and a wash-box system.
Belt-washing systems are highly effective for removing residual materials from conveyor belts, especially in settings where environmental or regulatory standards demand thorough cleaning.
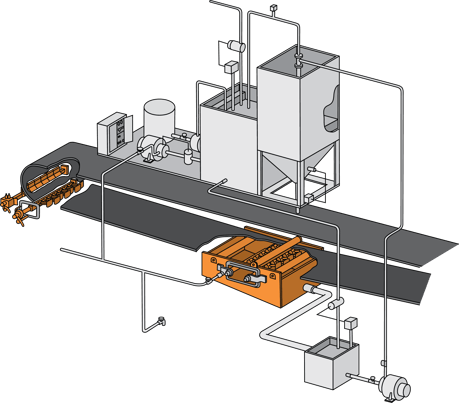
Typically, a wash box includes water-spray bars or nozzles that cover the width of the belt, followed by various belt-cleaning mechanisms like scrapers or rotating brushes. Subsequently, systems often incorporate belt-drying components such as pressure rollers, squeegee blades, or forced-air nozzles. Managing effluent discharge (the water and removed solids mixture) and handling water and debris separation, recycling, or disposal are also integral aspects of these systems. Enclosures, seals to minimize overspray, controls, and access for inspection and maintenance complete the setup.
The standard wash-box configuration involves one or two spray bars for water application, followed by two or three secondary belt cleaners of conventional design. Operators adjust cleaner angles and pressures externally through access doors on the enclosure.
Secondary belt cleaners or brush cleaners are used depending on belt conditions; brushes are more effective on heavily grooved or damaged belts where flat blades struggle. Brush cleaners, however, may require more water to prevent material buildup that would impair their function.
Traditionally, wash boxes were custom-designed due to varying conveyor specifications, material properties, and space constraints. Recently, modular wash-box systems have emerged, using standardized components and configurable modules. These modular units offer flexibility, ease of installation, and cost efficiency, allowing for easy adaptation as cleaning needs or budgetary considerations evolve. Modular setups enable components to be separated, accommodating structural obstacles or spatial constraints around conveyors.
When planning a wash-box system, a comprehensive analysis considers factors like conveyor layout, water recycling capabilities, energy requirements for drying, and the efficiency of solids separation. Detailed information on bulk material properties, carryback levels, and equipment choices informs decisions regarding water usage, belt cleanliness, moisture levels, and effluent management.
Specifications for a typical wash-box system include:
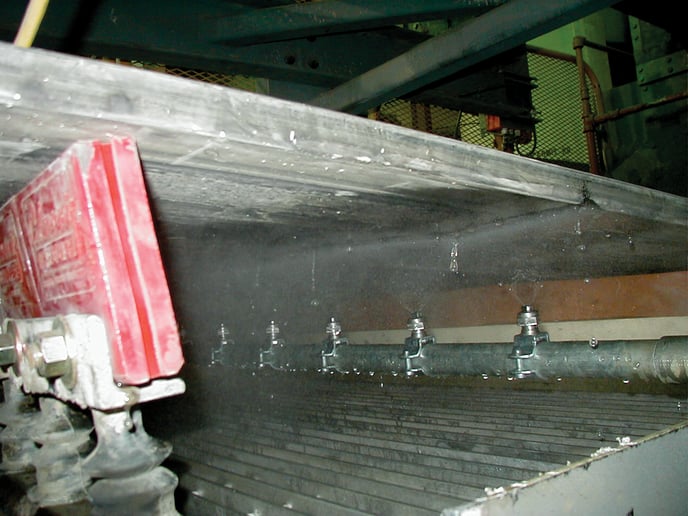
- Installation of a spray belt-washing system: The conveyor system will be equipped with a spray belt-washing system installed directly after the head chute to provide final removal of any residual cargo from the belt. This spray-wash system will be contained in a watertight metal enclosure fitted with water supply and an oversized drain.
- Sizing: The belt-washing system will be sized based on the amount and properties of expected carryback per square meter (/ft2) of belt.
- Water-spray bar: The enclosure shall be fitted with at least one water-spray bar with engineered nozzles that are positioned to wet the entire cargo-carrying portion of the belt and to flush removed material out of the box through the drain.
- Secondary cleaners: The wash box will be fitted with a minimum of two secondary cleaners to remove fines and water from the belt’s load-carrying surface.
- Access: The wash box shall be fitted with watertight access door(s) to allow easy inspection and service.
- Hold-down rollers: The spray-wash system shall include a minimum of three hold-down rollers above the belt that hold the belt in position against the spray-applied water and cleaning edges.
- Drain system: The volume and flow rate of flushing water and design of the drain system shall be sufficient to prevent settling of bulk solids in the drain system.