Conveyor Belt Damage
Understanding and Preventing Common Conveyor Belt Damage: A Comprehensive Guide
Impact Damage
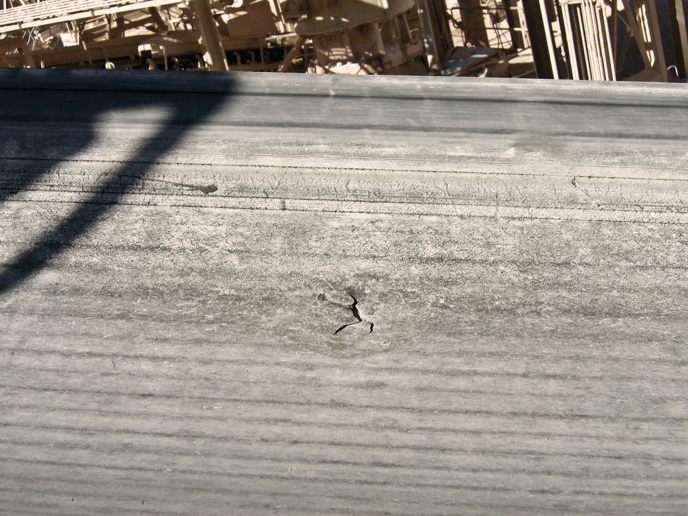
Impact damage to conveyor belts is primarily caused by large or sharp materials striking the
belt's top cover. For instance, frozen lumps of coal can nick, scratch, or gouge the surface, potentially leading to tears if the impact is severe. This type of damage is most commonly observed under crushers or in mining operations handling run-of-mine (ROM) materials. Additionally, long drops of materials onto the belt, especially without adequate energy absorption systems, can exacerbate impact damage. To mitigate the risks associated with impact damage, it is essential to implement measures that prevent large objects from reaching the belt and, when applicable, consider the use of impact-resistant belts or belt support cradles for enhanced durability and protection.
Entrapment Damage
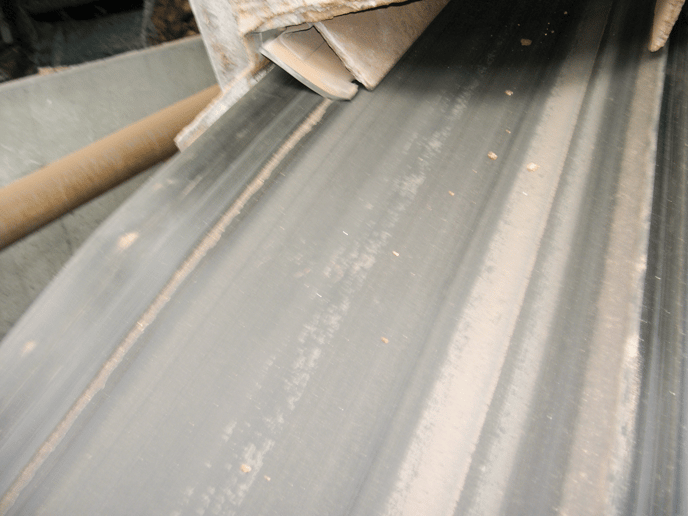
Entrapment damage typically manifests as grooves along the belt edges, near the area where the belt passes under the steel conveyor skirtboard. Often mistaken for wear caused directly by the skirtboard-sealing system, entrapment damage actually results from materials getting trapped beneath the sealing system due to belt sag. These trapped materials abrade the top cover as the belt tightens, leading to grooves and scalloping along the length of the belt under the skirtboard. Improper installation of wear liners and skirting can further contribute to this type of damage. This can be a challenging issue to diagnose accurately. To prevent entrapment damage, it is crucial to eliminate belt sag through proper support, in the skirted load zone. Additionally, using appropriately manufactured skirting designed for conveyor belts ensures that grooves are not the result of skirting-related issues but are rather mitigated through proper belt support.
Edge Damage
Damage to the edges of conveyor belts appears as fraying or wearing away of the belt material along its sides. This type of damage is primarily caused by belt mistracking, which can result from conveyor structures being out of alignment, uneven loading on the belt, or the accumulation of material on rolling components. Even minor factors like the differential effects of sunlight over time can contribute to belt mistracking. Technologies such as self-adjustment idlers and laser surveys are employed to identify and correct belt mistracking issues, preventing edge damage and ensuring efficient conveyor operation. In certain industries, regulatory agencies may cite edge damage as a potential hazard. Consistent monitoring of belt alignment and the implementation of tracking systems play crucial roles in preventing edge damage, safeguarding both operational efficiency and compliance.
Delamination
Delamination or Ply Separation occurs when the layers of the conveyor belt's carcass separate or detach from the top cover. This can be caused by excessive tension in the belt, foreign materials infiltrating the belt layers, or inadequate sealing against moisture and chemicals. The entry of foreign materials and environmental factors can weaken the bond between layers, leading to delamination and potentially compromising the structural integrity of the belt. In high-moisture environments, the belt’s carcass can absorb moisture, resulting in what is called ply separation. This absorption causes the carcass to swell and separate. Opting for molded-edge belts, though more expensive, can resist moisture absorption and prevent ply separation.
Worn Top Cover
The top cover of conveyor belts often shows wear in areas where materials are loaded onto the belt. Loading materials inherently causes abrasion on the top cover, gradually wearing it down. Carryback, where materials adhere to the belt after discharge and subsequently fall off at other points along the conveyor, can also contribute to top cover wear. Properly installed belt cleaners are crucial for preventing carryback and reducing top cover wear. However, poorly matched or improperly installed belt cleaners can themselves cause damage by applying excessive pressure or uneven cleaning, leading to accelerated wear of the top cover.
Rips and Grooves from Foreign Objects
Conveyor belts are susceptible to damage from foreign objects such as metal pieces or sharp materials left on the belt. These objects can create rips or grooves in the belt surface, posing significant operational hazards. Examples include packing-crate strapping or loader bucket teeth that can become wedged against conveyor components, acting like blades that slit or gouge through the belt material. Detection and prevention methods such as grizzly screens, metal detectors, and video monitors are employed to mitigate the risk of foreign object damage, though complete prevention remains challenging due to the unpredictable nature of these incidents.
Belt-Cleaner Damage
Belt cleaners are essential components for extending the service life of conveyor belts by removing debris and preventing material buildup. However, improperly installed or maintained belt cleaners can cause damage to the belt's top cover. Issues such as excessive blade pressure, improper blade-to-belt contact, or blade chatter can lead to accelerated wear and tear on the top cover. Despite their role in preventing material buildup, belt cleaners must be carefully selected and maintained to minimize their impact on belt integrity.
Top-Cover Cracking
Top-cover cracking occurs when conveyor belts are subjected to excessive strain due to incorrect belt types for the pulley sizes used. The strain can cause the rubber in the top cover to crack perpendicular to the direction of belt travel, exposing the reinforcing materials underneath. This type of damage highlights the importance of matching belt specifications to pulley diameters and operational requirements. Installing a thicker belt to mitigate other types of damage, such as impact resistance, can backfire if it exceeds the recommended pulley diameter limits, leading to premature top-cover cracking. To prevent this issue, it is imperative to ensure that the selected belt size aligns seamlessly with the dimensions of the pulley, preventing undue stress and potential damage.
Heat Damage
Conveying hot materials can cause the top cover of conveyor belts to crack or the belt plies to separate. This is called heat damage. The severity and direction of cracks depend on the temperature and type of material being conveyed. Some belts are specifically designed to withstand high temperatures, but in general, it is crucial to allow materials to cool sufficiently before loading them onto the belt. Proper heat management is essential to prevent heat-induced damage to conveyor belts and ensure their long-term reliability. Heat damage poses challenges to cleaning procedures as the cracks make it difficult for belt scrapers to reach certain areas. While some temporary fixes exist, such as splicing or epoxy applications, the best preventive measure involves selecting belts designed to resist heat damage.
Junction-Joint Failure
Junction-joint failure occurs at transitions where the belt shifts from a flat profile to a troughed profile. The outer portions of the belt must stretch more than the center portion, which can lead to damage at the junctions where wing rollers meet flat rollers. This damage appears as stretch marks or tears running parallel to the belt's length. Recognizable through improper wear on the return roll, this failure can escalate, eventually causing the belt to split into thirds. Factors such as inadequate transition distances, excessive tension, or improper idler spacing can exacerbate junction-joint failure. Proper design and maintenance of transition zones are critical to preventing this type of damage and ensuring smooth conveyor operation. To mitigate this, careful consideration of the transition distance, based on belt specifications and trough angles, is essential during the belt selection phase.
Cupping
Belt cupping refers to a permanent curvature across the width of the conveyor belt, perpendicular to its direction of travel. Cupping can be caused by factors such as excessive heat exposure, improper transition distances, or too severe a trough angle for the belt type. Over-tensioning of the belt or the presence of certain chemicals can also contribute to belt cupping. Over-tensioning can be identified by observing the belt (without cargo) lifting out of carrying idlers when the belt should typically settle into the troughs. Cupped belts are challenging to track due to reduced frictional contact with rollers, affecting conveyor efficiency and requiring careful monitoring.
Camber
Belt camber, on the other hand, refers to a curve across the length of the belt. Improper storage, handling, splicing, or tensioning during installation can lead to belt camber. Cambered belts can cause slow side-to-side movements during operation, often mistaken for belt mistracking caused by other factors like misaligned splices. Adhering to recommended storage practices, such as storing belts on racks or through their core and rotating the belt every 90 days, is critical to prevent camber-related issues and maintain optimal conveyor performance. Proper storage, handling, and installation practices are essential to prevent belt camber and ensure smooth conveyor performance.