Proper Conveyor Design = Efficient Material Handling
Enhancing Material Handling Efficiency through Advanced Conveyor System Design
Achieving a conveyor system that operates safely and efficiently in industrial facilities or mines necessitates meticulous design. Despite best efforts, it's challenging to completely eliminate fugitive materials due to factors like initial design flaws, inadequate maintenance, bulk material variability, conveyor overloading, and component wear.
Numerous design elements play crucial roles in minimizing fugitive materials. These include integrating dust-resistant structures, optimizing skirtboard designs, employing external wear liners, choosing appropriate pulley sizes, and implementing effective belt tracking solutions. Ensuring a clean work area devoid of utility components and planning for future upgrades are also essential considerations for enhancing material handling operations.
Innovative technologies offer additional avenues for material control in conveyor systems. Advanced solutions such as engineered flow chutes, air-supported conveyors, and belt washing systems can significantly improve operational efficiency. Furthermore, modern 3D drafting and fabrication techniques enable flexible component arrangements without substantial cost increases. A straightforward approach involves orienting components to minimize flat surfaces where fugitive material can accumulate.
Structural Design for Minimizing Fugitive Materials
Maintaining cleanliness around conveyors is critical, necessitating the elimination of areas prone to material buildup to simplify cleaning procedures. Horizontal structural members should ideally be angled at 45 degrees to facilitate material shedding, reducing the need for crew members to reach under the belt to remove debris.
For areas where dust buildup is unavoidable, incorporating dust plates or caps on structural members can effectively minimize accumulation in hard-to-reach spots. Deck plates and drip pans should be designed to direct material outward, facilitating the collection of fugitive material. Vibration applications can further assist in preventing dust buildup and ensuring materials flow away from the conveyor.
Optimizing Skirtboard and Wear Liner Design
Skirtboard height recommendations, as outlined by the Conveyor Equipment Manufacturers Association (CEMA), should consider the size of the largest material lumps conveyed without covers. Today, many skirtboards are covered to contain dust, necessitating designs that allow airflow above bulk materials. This often requires heights at least twice those recommended for open-top skirtboards, with tops designed to prevent material accumulation through significant pitch adjustments.
Traditionally, wear liners have been mounted inside vertical metal skirtboards, positioned between bulk materials and the metal structure. However, this setup can lead to wear liner failures and belt damage if incorrectly installed, complicating inspection and replacement due to confined spaces. Repositioning wear liners to the outside of skirtboards simplifies maintenance, allowing for easier inspection, accurate installation, and quick replacement. Adjustable wear liners and modified skirt seal clamps further enhance installation accuracy and structural integrity.
Pulley Sizes
For decades, tail, bend, and discharge pulley sizes have been determined using tables from belting manufacturers. These tables specify minimum diameters to minimize costs and ensure belt safety. When selecting pulley sizes, it's crucial to consider accessibility for servicing. Larger diameter pulleys, such as those with a minimum diameter of 600 millimeters (24 inches), provide ample space between carrying and return runs. This space accommodates the installation of a tail pulley protection plow and, if needed, a return belt plow. It also facilitates easier plow inspection and provides sufficient room for plows to eject fugitive materials from the belt.
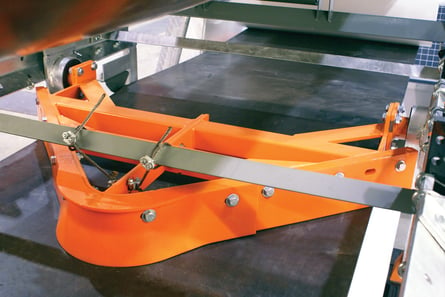
Additionally, a larger head pulley at the belt discharge creates the necessary room to install belt cleaners in the optimal position. Despite the higher initial cost, these larger pulleys lead to savings by effectively controlling fugitive materials, reducing downtime, and minimizing maintenance.
Indexing Idler
Belt mistracking significantly contributes to spillage, necessitating effective belt training. To minimize costs, many new installations opt for training idlers instead of belt training devices. However, these idlers often end up tied off to one side to compensate for belt misalignment or to protect them from excessive wear caused by continuous off-center running.
Conveyor belts can veer off-course due to several factors, including off-center loading, misaligned conveyor structures, component alignment issues, and weather conditions. Tying off training idlers with loose wire or rope poses safety hazards near moving belts, exacerbated by changes in operating conditions requiring idlers to be repositioned multiple times a day.
To mitigate these risks, idlers can be equipped with indexing mechanisms that lock them into position without relying on unsafe tie-down methods. This approach ensures the belt remains properly aligned without compromising safety or efficiency.
Conduit and Piping
Conveyors serve as convenient pathways for utilities and electrical components. Over the years, these conduits and piping have been installed without sufficient consideration for their impact on conveyor installation, maintenance, and operation. This oversight is particularly evident in discharge and loading zones, where utilities can obstruct access to critical conveyor components, such as plows designed to eject foreign objects.
To optimize functionality and safety, utility conduits in these zones should be strategically placed to avoid interference with essential components for controlling fugitive material. Main conduits can be positioned overhead, with flexible drops where necessary to power or communicate with components. Along the conveyor's carrying run, supporting conduits on the structure is feasible, provided they do not impede service access or compromise component effectiveness.
In conclusion, prioritizing thoughtful design considerations such as pulley sizing, belt tracking methods, and conduit placement enhances the efficiency and safety of conveyor systems. By addressing these factors, industries can achieve smoother operations, reduced maintenance costs, and improved overall productivity.