Are You Regularly Walking & Inspecting Your Conveyor Belts?
Comprehensive Conveyor System Assessment
Details of conveyor systems often fade over time, with specifications and component information frequently lost amid changes in plant ownership, management, and personnel responsibilities. As equipment evolves through replacements and improvements, crucial "nameplate information" about components may become outdated or solely retained by individual memory. Conducting a comprehensive belt conveyor system survey emerges as vital, not only for maintenance but also as a fact-finding mission to enhance system performance, reduce operational costs, and bolster safety.
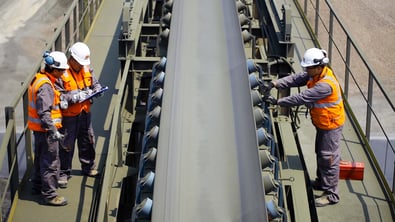
The initial belt walk requires meticulous data collection, often necessitating involvement from suppliers, contractors, or consultants to conduct a thorough system census. Specialized equipment may be essential for accurate data capture, minimizing return trips for missed details like dimensions or serial numbers.
Tool Functions for Site Survey
- Personal Protective Equipment (PPE): Ensures personal safety during surveys.
- Anemometer: Measures air velocities for dust suppression.
- Angle Finder: Documents structure inclines.
- Decibel Meter: Assesses noise levels.
- Durometer Reader: Evaluates conveyor belt and skirtboard seal hardness.
- Infrared Thermometer: Records component temperatures.
- Level: Checks component alignment.
- Soap Stone: Temporarily marks steel components.
- Tachometer: Measures belt speed.
- Tape Measure: Determines distances.
- Flashlight: Allows inspection of dark or enclosed areas.
- Camera: Captures visual data.
- Pencil & Paper: Records findings.
- Tool Belt/Harness: Safely carries equipment.
Recording and Archiving Information
During the conveyor system census, critical manufacturer, model, and specification data are recorded and archived centrally within the plant's maintenance files. This data encompasses a wide array of system details:
Centralizing Information
It's prudent to consolidate this information into a centralized library that includes maintenance manuals, service procedures, parts lists, operating instructions, supplier details, and drawings related to the belt conveyor system. This centralized digital repository can integrate with a computerized maintenance management system (CMMS), facilitating swift access for both plant personnel and contractors, thereby streamlining maintenance operations.
Specialized Services and Updates
Certain maintenance contractors and suppliers offer specialized data collection services, which can be integrated into routine assessments or implemented separately as part of CMMS selection and deployment processes. Regular updates to system data, including original design information and change records, are essential practices to maintain accuracy and effectiveness in ongoing maintenance cycles.