How To Guard Your Conveyor Belts & Protect Workers
While it may not be a government requirement, the belts should be guarded along walkways to prevent unwary employees from becoming trapped in the moving conveyor.
Simply walking up the walkway offers risks that could lead to fatality: Walkways close to the conveyor provide areas where employees can become entrapped in the conveyor. There have been instances in which employees slipped on a walkway and then became entangled in the conveyor, simply by trying to break the fall or catch their balance.
While it may not be a government requirement, the belts should be guarded along walkways to prevent unwary employees from becoming trapped in the moving conveyor.
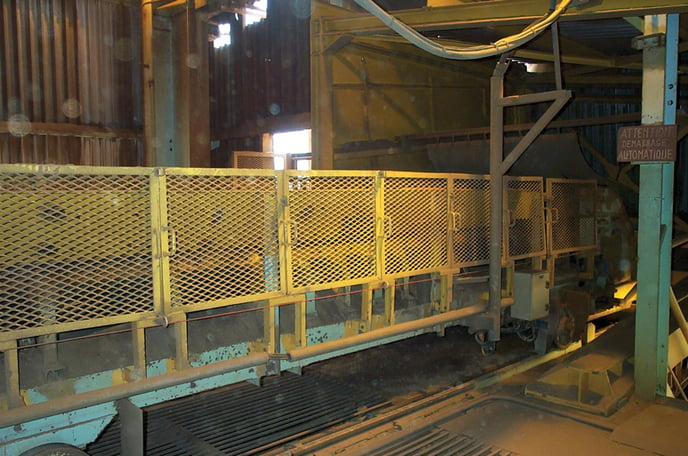
It is important that guards be provided at every dangerous part of a conveyor normally accessible to personnel. Hazards are considered to be guarded by location if they are located a sufficient distance above the ground or walkway to prevent contact.
The challenge to designing and installing effective guarding is to protect operations and maintenance personnel without interfering with the operation of the plant. A well-designed barrier guard will prevent personnel from reaching moving machine parts, yet its size and shape will permit the safe handling of the parts during removal or replacement (when the guard has been removed or disabled and the conveyor locked out / tagged out / blocked out / tested out.)
Typically, barrier guards require a tool for removal and may include a sign indicating which equipment should be isolated (that is, locked out / tagged out / blocked out / tested out) before the guard can be removed. Visual inspection of conveyor components and access to lubrication points should be possible without the removal of the barrier guards. Barrier guards may be hinged, allowing them to be moved out of position, or they may be bolted in place. They should be constructed of materials that are both wear—and corrosion-resistant, and they should be able to withstand the vibration of system operation.
New Technology in Guarding
In many facilities, conventional physical barriers are being replaced with newer technologies that monitor area perimeters and detect entry into hazardous areas.
However, these newer technologies, such as laser beams and infrared light curtains, are effective only when power is on, and they can be fooled by someone determined to gain entrance into a secure area. These systems require care and good maintenance in order to be reliable. For example, they might not function well where airborne dust can settle onto the electric eye receivers. It is wise to have mechanical access control systems as redundant or backup systems, as a failure of the “high-tech” devices may not be obvious.